Custom Porous Sparger Supplier
As an ISO certified company, Filson always provides you reliable porous sparger.
- Customized materials and sizes available
- Allowable to clean and reuse
- Easy to install and replace
- Robust and all-welded construction
- Multiple series suitable for almost all liquids and gases
What is Porous Sparger
Filson porous sparger, also known as sintered sparger, is ideally designed to transfer gas into liquids effectively. Porous sparger is usually made of metal powder through a sintering process.
Filson porous sparger includes various categories, like liquid sparger, gas sparger or tank sparger. We can also fabricate porous sparger to work with different gases, such as ozone sparger, CO2 sparger, nitrogen sparger, oxygen sparger, ammonia sparger, etc.
Comparing with conventional sparger, the designed micron rating of our porous sparger ranges from 0.2 to 100 micron (typically 0.5 to 12 micron). Therefore, Filson porous sparger has lager contact surface area to create more tiny bubbles.
Porous Sparger Series
With uniform and various pore design, Filson liquid sparger can produce bubbles with diameter down to 0.1 micron in a parallel flow and counter-current. This sparging process can remove other dissolved gas or volatile liquid from liquid through creating gas bubbles.
Owing to the good compatibility and strong mechanical strength, Filson gas sparger is best suited for many types of gas, like CO2, nitrogen, ammonia, etc. With different porosity of gas sparger design, Filson can provide you coarse and fine gas spargers to meet your applications.
Filson tank sparger, also called in-tank sparger, is often used to fermentation, agitation, de-watering or other applications. With 2 to 10 micron rating design, the flow rate of our tank sparger has increased 3 to 4 times lager compered with other spargers.
Porous Sparger Types by Gas Classification (5)
Porous Sparger Related Products (4)
Porous Sparger Benefits
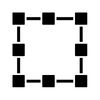
Filson porous sparger has high micron rating design usually up to 12 micron. Hence, it has large transfer surface area almost 8-10 times than conventional sparger.
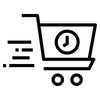
To ensure a quick delivery, Filson will choose Fedex/TNT/DHL or other transportation ways based on your requirements.
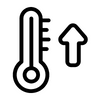
Utilizing stainless steel, nickel or other alloys, our porous sparger can withstand high temperature up to 787℃. Besides, it can also work under high corrosion condition.
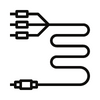
As an essential part in porous sparger, we can provide you multiple connectors to choose, like NPT threads, straight tube, flange or sanitary connections.
Advantages of Porous Sparger
Using a high-quality and high-efficiency porous sparger, you will get following advantages:
- Durability: Filson porous sparger can be easily cleaned through both chemical and physical methods like ultrasonic cleaning. Hence, it can serve you normally for several years through regular cleaning.
- High Porosity: The general porosity of Filson porous sparger ranges from 15% to 55%. For this reason, our porous sparger can transfer gas into liquid more efficiently.
- Multiple Size: Filson is able to make porous sparger with a range from 6’’ to 48’’, and the standard diameter is 0.5’’ and 1’’. You are allowed to send us your customized specifications on porous sparger.
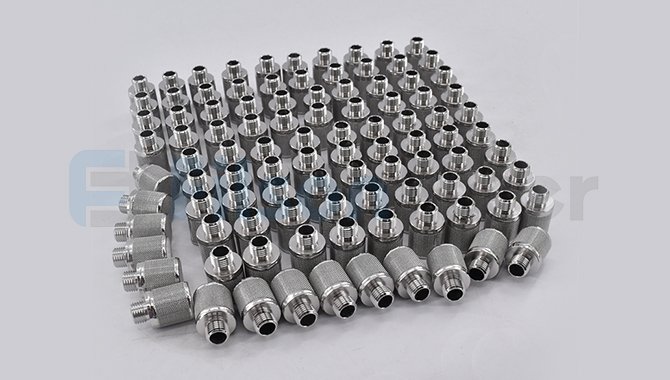
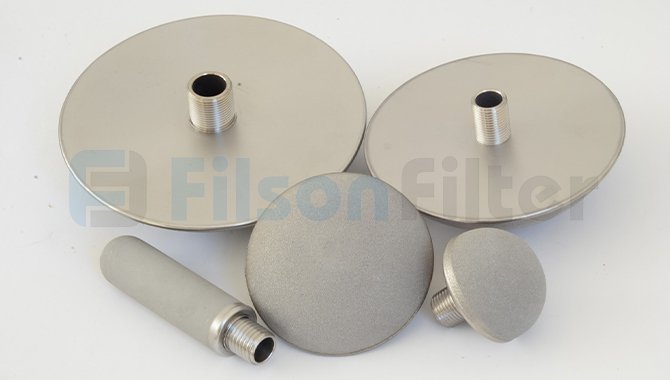
Porous Sparger Specific Features
Filson porous sparger possess the following characteristics to support a smooth gas-transferring.
- Working normally under high pressure up to 3.4MPa
- Reduced cost due to lowering gas or liquid consumption
- Able to generate uniform and fine bubbles with 0.1 micron diameter
- Wide micron rating ranging from 0.2 to 100 micron
- OEM service to offer customized shapes, sizes or materials
- Huge capacity up to 100 m3/h
- Lager flow rate up to 30 GPM
- Reliable quality in accordance with ISO certification
Why Choose Filson Porous Sparger
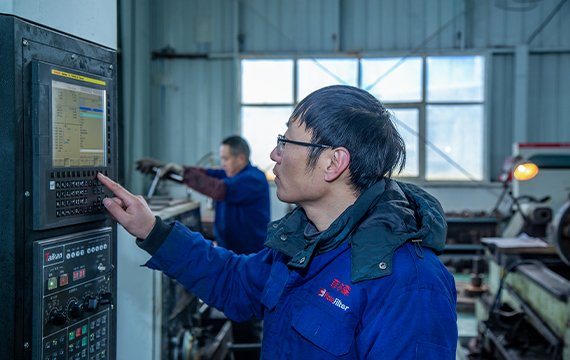
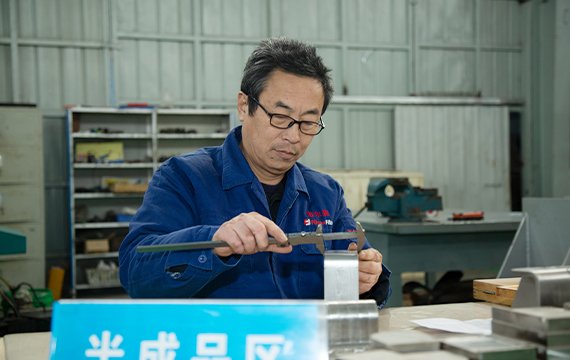
Filson porous sparger can be fabricated into wide porosity with a range from 15% to 55%. This design guarantees larger contact area and improve efficiency of introducing gas into liquid.
Filson always uses a variety of metals to fabricate porous sparger, just like sintered metal sparger. Therefore, it has high temperature tolerance up to 787℃ and corrosion resistance. And porous sparger is widely applied in chemicals, fermentation, water treatment or other industries.
Having more than two decades experience on making porous sparger, Filson has the latest technology, advanced equipment, professional technicians and skilled workers. We promise to offer you satisfactory porous sparger with a competitive price.
If you are interested in our porous sparger or want to learn more details, please give us a call at +86-157 3695 8886 or send us an email at sales@filsonfilters.com.
The general specifications of porous sparger are as followed. You can choose from them or just send us your specific data.
- Raw Material: stainless steel 304, 316L, monel, nickel
- Operating Temperature: up to 787℃
- Differential Pressure: up to 3000psid
- Working Pressure: up to 3.4MPa
- Common Length: 6’’ – 48’’
- Standard Diameter: 0.5’’, 1’’
- Porous Element length: 1’’ – 4’’
- Micron Rating: 0.2 – 100micron (typically 0.5 – 12micron)
- Connection: NPT threads, straight tube, flange, sanitary connections
- Thread Size: 1/8’’, 1/4’’, 3/8’’, 1/2’’, 3/4’’, 1’’, 2’’
To meet our customers’ different applications, we offer OEM service and multiple materials to fabricate porous sparger as follows:
- Stainless steel 304, 304L, 316L, 347, 430
- Inconel 600
- Monel 400
- Nickel 200
- Hastelloy C-276
- Polypropylene
- Ceramics
- Glass
- Other alloys as customized
Applications of Porous Sparger
With fine accuracy usually ranging from 0.5 to 12 micron, Filson sparger can create smaller bubbles than traditional spargers. And it can be used in fermenter, like wine production, to improve cell growth in fermentation reactions by sparging oxygen.
Having better chemical properties, Filson air sparger can be better used in bioreactor. Our sparger will offer sufficient air or pure oxygen for bioreactor, so this reaction created by enzymes or organisms will be improved.
Filson porous sparger, mainly used to transfer gas into liquid, can be widely applied in food and beverage industry. For example, through introducing CO2 to beer, the beer’s life will be extended. And sparing nitrogen to replace oxygen, juices and oils will have long life.
With high porosity up to 55%, our porous sparger can generate more gases than common sparger. So it is ideally used in fish ponds or aquarium to introduce oxygen. By using our porous sparger to create oxygen, pulp and paper will be bleached efficiently.
Filson always use safe and non-toxic metals fabricate porous sparger. When you need a sparger in pharmaceutical industry, you can choose ozone sparger. Through sparging ozone, water systems will be sanitized with less adverse effects.
With porosity design ranging from 0.5 to 12 micron, our porous sparger can realize high efficiency of transferring gas into liquid. Using it in green chemical industry, more and high-quality oxygen can be created in order to maximize availability of oxygen with minimized cost.
Microalgae is widely used in cosmetics, food supplements or pharmaceutical industry as a raw material. Porous sparger is an ideal choose to increase the production rate of microalgae biomass and products in a photobioreactor. Therefore, you can obtain large profits with less costs.
You can use Filson porous sparger to sparger hydrogen for a series of hydrogen chemical reaction processes, like hydrogen water filter and hydrogen rich water maker. Furthermore, nano-sized hydrogen bubbles will be generated, making it easier to combine with water molecules.
Porous Sparger: The Ultimate FAQs Guide
This guide covers everything you’re looking for about porous sparger such as working principle, function, benefits, features and classification, among other vital aspects.
So, if you want to be an expert in porous sparger, read this guide.
A porous sparger is a device that you can use to introduce gas into liquids in different process applications.
Porous Sparger
The main function of a porous sparger is to efficiently introduce gas into liquids.
It has thousands of tiny pores which release numerous and tiny bubble of gas into the process liquid.
Porous spargers create more and smaller gas bubbles than any other type of sparger, hence increasing the surface area of gas/liquid contact.
As a result, they significantly lower the quantity of gas and time required to distribute the gas bubbles in the liquid.
The porous sparger has a network of pores that produces numerous tiny bubbles when you pass pressurized gas through it.
The bubbles usually range between 0.5 to 10 micrometers and facilitate the efficient mass transfer of gas into liquids.
You can use porous spargers in many industries to perform limitless operations in a wide range of applications.
These devices can be configured into different shapes and sizes to meet the demands and special needs of specific industries, processes, and applications.
Customized sizes and shapes can be fit with additional hardware to meet your special sparging conditions upon request.
Some of the processes and applications which require the use of a sparger include:
Porous sparger
- Carbonation: Introduction of carbon dioxide gas in beverages and beer for preservation
- Aeration: Used for waste streams to meet biological oxygen demand
- Bioremediation: Introduction of air to facilitate the proliferation of bacteria in waste treatment
- Agitation: Use in diverse industries to facilitate efficient mixing of different liquids in a tank/vessel.
- Fermentation: Sparging oxygen to enhance the growth of cells incubated under fermentation conditions
- Oxygenation: Introduction of oxygen in fish ponds or aquarium
- Ozonation: Sparging ozone for ultra-purification of water systems in pharmaceutical industries
- Oxygen bleaching: Sparging oxygen to bleach pulp when manufacturing paper
- Oxygen stripping: Used in the manufacture of edibles wines, juices, and edible oils where nitrogen sparging replace oxygen to enhance product longevity.
- Hydrogenation: Sparging hydrogen for a broad range of hydrogen chemical reaction processes.
- Dewatering: Important in the motor industry for the removal of entrained water from motor oil through sparging nitrogen.
- Oil flotation: Removing water produced from oil wells through sparging in nitrogen or air.
- Gas/liquid reactions: Used to improve process performance through sparging in oxygen, air, and other gases into the reactors.
- pH control: Adjusting pH of a process stream or wastes through sparging ammonium gas or carbon dioxide.
- Chlorine bleaching: Sparging chlorine to bleach pulp when manufacturing paper
- Column floatation: Floatation of coal and separation of other solids through sperging air
- Bulking: Introduction of nitrogen through sparging when bulking mustards or salad dressings.
- Stripping volatiles: Removal of volatile organic compounds from waste streams through sparging air
- Steam injection: Elimination of steam hammers and for direct heating through sparging steam.
When ordering the porous sparger for your application, you should select the sparger keeping in mind the type of process application you intend to use the sparger on.
Static spargers are used for tank/batch processes while dynamic spargers are designed for continuous applications in channels or pipelines.
Porous spargers come in a variety of designs such as perforated pipes, rings, frames, plates, and grids.
A porous sparger contains the sparger elements that produce the tiny bubbles and the attachment base that connects to the gas lines.
Using a quality and high-efficiency porous sparger will confer the following advantages:
- High efficient and gentle transfer of a large quantity of gas into the liquid
- Increased gas-liquid contact area
- Lower volume and time required for the liquid to dissolve the gas
- Reduced cost of operation due to less time and fluid volume
- Cleanable and reusable
- Enhanced rate of diffusion
- Homogeneous and defined gas distribution
- Reduced energy cost as a result of lower gas consumption
You can make your porous sparger from diverse types of construction materials.
The choice of the most suitable material will depend on the operating temperature and pressure, flow rate, corrosive effects of the fluid and gas, etc.
Generally, the majority of porous spargers are constructed using stainless steel (SS) 316L.
However, you request porous spargers constructed from polypropylene, sintered porous polyethylene, ceramics, glass, SS 304L, SS 347 SS, SS 430, Monel, Nickel, and other alloys.
Higher metal alloys like Hastelloy and Inconel are suitable for making porous spargers that operate under very high temperatures and aggressively corrosive conditions.
Porous metal spargers are stronger and more resistant to mechanical shock compared to other brittle materials which can break due to pressure.
You can also make your metal porous spargers using metal powder medium, metal fiber, or mesh for optimal economics.
There are different types of porous spargers including:
· Static Porous Spargers
Static porous spargers are tank spargers used to introduce gas in liquids inside the tank or vessel.
You can use in-tank spargers in both batch and continuous processes in tanks that have or luck agitation.
A single porous sparger is usually sufficient for applications having a small tank.
For large tanks, you will need to manifold several porous spargers together in a linear or radial pattern.
You should use reinforcement when your tank is agitated.
· Dynamic Porous Spargers
Dynamic porous spargers are designed for use inside the pipeline.
They include:
- In-line (Non-intrusive porous spargers
- Sidestream porous spargers
- Tangential (intrusive porous spargers)
The design of a good porous sparger should support the efficient distribution of gas into liquids at the most profitable production cost.
A high-quality porous sparger should possess the following characteristics to support a smooth transfer gas.
- The material of construction should be non-corrosive and able to withstand extreme temperatures.
- The design of the connectors and diameter of the sparger should meet the requirements of the application.
- The material should withstand strong mechanical shocks
- It should be compatible with additional hardware that might be required by some special types of applications.
- It should be easy to install and replace
- Should be easy to clean
- The construction should a robust and high quality, all-welded construction
- Uniform and fine pore sizes help in the mass distribution of tiny gas bubbles
- Should have a broad range of media pore sizes to enable control of the bubble size
- Should be available in a variety of standard and customized shapes and sizes
- Should have sanitary furnishings if required
Designing a customized porous sparger can be challenging if you fail to pay attention to the critical aspects which directly affect the effectiveness of the device.
You can follow these tips to help you fit your porous sparger to the needs of your application.
Gas sparger
· Know your Goals and Application Details
You need to exhaustively outline the project output you expect to achieve and the details of your process application.
You should answer the following questions exhaustively.
- What is the nature of your application? Are you carbonating, controlling pH, oxygenating, etc.?
- What are the properties of your liquid and gas?
- Is it a batch or continuous application?
- What are the flow rates, pressure, and temperature of your system?
- At what speed do you want the gas dissolved in the liquid?
· Work Out the Actual Volume of Gas you need to Disperse into the Liquid per Minute
You need to determine the actual cubic feet per minute (ACFM) that your sparger must supply into the liquid.
You can calculate this from the standard CFM and gas temperature and pressure.
· Determine the suitable Gas Exit Velocity
Determining the optimal gas velocity is essential and helps avoid the coalescing effect.
When gas coalesces, the bubbles grow in size, they lose the surface area, which increases the number of bubbles you require to achieve the desired distribution.
Consequently, you will use more gas and energy to achieve the same level of sparging.
Optimal velocity will help you conserve precious gas and save on energy cost as a result of reduced or no coalescing effect.
· Determine the Required Sparging Surface Area
The sparging surface area depends on multiple variables that are application-specific.
The aspects of the total surface area will influence the number, shape, and size of porous spargers your system will need.
You can consult a professional to help you determine the most suitable surface area for your application systems.
· Determining Geometry and Inclusions of the Sparger
This is the final step in designing a sparger and will take account of intricate details to meet the demands of your typical application.
Consider the most appropriate material to construct your porous spargers, the ideal media grade or pore sizes, the dimensions of the sparger, and the number of sparger elements required.
You can collaborate with our engineers to help you come up with the most efficient sparging elements at a reasonable budget.
The size of a porous sparger injector is calculated based on the gas exit velocity.
You have to maintain the velocity below the maximum velocity for the continuous production of small bubble sizes.
Inline spargers located inside the pipelines can supports higher gas flowrates because the pipeline force can shear off bubbles from the injector.
The temperature and pressure of the liquid indirectly affect the sizing of the sparger since they influence the actual cubic feet per minute.
Porous spargers have numerous beneficial properties compared to other types of spargers constructed from drilling pipes and other similar devices.
Porous spargers offer a smooth and efficient entrance of gas bubbles into the liquid through the creation of hundreds of thousands of fine bubbles.
As a result, you save a lot of money and time because the smooth mass transfer of gas reduces the volume and time required to dissolve the gas.
On the contrary, drilled pipe spargers and related devices offer a harsh and inefficient transfer of gas bubbles into the liquid.
The drilled sparger also produces large bubbles that increase the gas/liquid contact area and time required to dissolve a unit volume of gas.
Since the drilled gas spargers produce large bubbles, you will need a higher volume of gas that translates to the increased cost of production.
The on-stream service life of a porous sparger significantly varies depending on the material of construction and frequency of use.
Porous spargers constructed using all-metal construction materials can serve you for several years even under oxidizing environments at temperatures above 1450°F.
Porous sparger
The gas distribution efficiency of a porous sparger depends on numerous factors.
Some of the most critical factors that directly affect performance include:
- The contact time between liquid and gas
- The pressure of the gas
- Temperature and pressure of the liquid
- Size of the bubbles
- The flow rate of gas compared to the flow rate of the liquid
- The gas exit velocity
- The actual ability of air compressor
A porous metal sparger is more reliable with a proven performance record compared to spargers constructed using other materials.
You should consider using porous metal sparger because it provides the following distinct advantages:
- Durable: Porous metal spargers can maintain useful service life for years of efficient sparging due to high structural integrity compared to other materials.
- Strength: Porous spargers constructed from metallic material possess unmatched tensile strength which makes it conducive for applications that work under high flow rates and pressure.
- Even porosity: Sintered metals favors the construction of porous spargers with uniform pore sizes that are evenly distributed. The availability of different grades of media with diverse pore sizes enables you to control the size of bubbles produced.
- Reusability: You can restore the efficiency of a metallic porous sparger to near original condition through appropriately scheduled cleaning. You can clean the media using a back pulse technique or other suitable methods.
- Thermal tolerance: Robust construction accompanied by perfectly welded seams and joints can withstand very high temperatures even under oxidizing atmospheric conditions.
- Availability of wide choice of materials: Other than stainless steel, you can also choose from a wide variety of different types of metals that can meet the project specifications.
Selecting a porous sparger which has the most suitable properties helps attain the best sparging results at a reasonable cost of production.
When choosing a porous sparger, you should ensure that it meets the following properties.
- The material of construction should be tolerant to the corrosive properties of the gas and process liquid.
- The mean pore size should be capable of producing the desired sizes of bubbles.
- The pores should be evenly distributed to enable fast and efficient mixing of gas into the process liquid
- The material of construction should meet the cleanliness requirements for sanitary processes.
- The sparger should have high tensile strength. It should be able to withstand high mechanical shock and maximum process temperatures.
- You should also ensure that the porous sparger can withstand the operating pressure of your system
Yes, you can clean a metal porous sparger through different techniques.
The most suitable method will depend on the frequency of use and types of liquids and gases being processed.
You can determine the number and sizes of bubbles produced by a porous sparger through video analysis technique.
Porous media for the construction of porous spargers have different classification schemes.
The two most important classification schemes are the ASTM and ISO classification schemes.
Accordingly, both standards classify the porous material into four different classes graded as extra coarse, coarse, medium, and fine.
The classes depend on the pore size of the porous medium.
For instance, ISO 4793 standards classify extra course material from 100 to 250 microns, Course from 40 to 100 microns, medium from 16 to 40 microns, and fine from 10 to 16 microns.
On the other hand, ASMT classification is stricter.
The fine group has porous materials with pore sizes ranging from 4 to 5.5 microns, medium from 10 to 16 microns, coarse from 40 to 60 microns, and extra course from 10 to 220 microns.
Sparging steam for in-tank heating has shown some weaknesses in several process applications. These include:
- Rough operations: Poor mixing and condensation can result in violent vibration and steam hammer.
Uncondensed steam will collapse when they contact a cold pipe that creates room for water to rush in and fill the void.
Pressure from the water will cause a pinging noise or steam hammer and vibration under severe conditions.
- Energy loss: Direct energy loss can arise from uncondensed steam causing a reduction in efficiency and increased demand on the amount of steam required to heat the fluid.
- Inefficient temperature control: When uncondensed steam escapes into the atmosphere or condense downstream, the steam energy does not register in the temperature controller. The condition can cause overheating of the liquid or variations in temperature.
- Hot zones: The porous sparger can create a hot zone around it that might burn materials that are sensitive to heat.
- Clogging: The pore in the sparger should be large enough to avoid being clogged by concentrated solids in columns bottom.
They should also withstand the long periods of operation demanded by industrial setups.
However, reducing the size of pores for smaller bubbles and preventing clogging is still problematic.
Therefore, these challenges may restrain the efficiency of porous spargers to small scale or laboratory tests rather than full-scale operations.
- Shutdowns: You also have to shutdown the flotation operations to carry out servicing and repair and also to enable slurry to penetrate the air system.
As you can see, there are many factors you should consider when buying porous sparger.
The best part, this guide as makes everything simple and easy to understand.
For questions or inquiries about porous spargers, contact FilSon Filters now.