Custom Sintered Metal Filters Based On Your Need
Filson designs and manufactures high performance sintered metal filters and filter material products for all industries, such as sintered metal fiber felt, multi-layer sintered wire mesh, stainless steel sintered filter, porous metal filter and specific material filter like sintered nickel filter.
Filson products have been widely used by many leading industrial companies in petrochemical industry, fine chemical industry, water treatment, pulp and paper making, automobile industry, food&beverage, metal processing and other industries. The independence, experience and expertise of Filson allow us to provide you with objective advice and customized sintering solutions.
Compared with the ordinary metal woven mesh, Filson sintered filter has excellent strength, long service life and good corrosion resistance. Also, we can provide custom sizes, materials, and layered configurations to meet your specific specifications.
Please send us your media type, flow, filtration accuracy, material requirements, and even ideal other brands of sintered metal filter, such as Mott filter, GKN sintered metal filter, Norman sintered metal filter, we will immediately quote for you.
Sintered Metal Filter
Sintered Metal Filter Advantages
Compared with other types of filter materials (e. g., stainless steel wire mesh, ceramic, glass fiber, filter paper), Filson sintered metal filter has higher mechanical strength and compressive strength. Whether in extremely high or low temperature experience, Filson sintered filter will provide you with excellent filtration performance.
- Easy forming, machining, welding and cleaning
- Available in filtration accuracy from 0.2 to 1000 micron
- High strength for cleaning and use multiple times
- Custom service for wide range of material and dimensions
- Commonly used in-200℃ ~ 650℃and acid, alkali corrosion environment
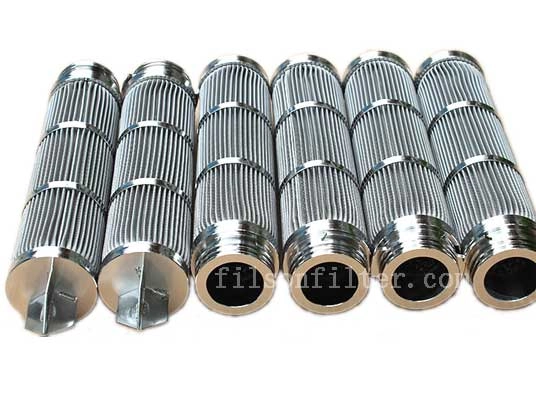
- Gallery
- Advanced Technology
- Features & Benefits
- Application
- High precision, high particles removal efficiency with accuracy between 0.5-300 um
- High-temp resistance, all sintered metal construction can withstand high temperatures, maximum 1000°C
- Easy to be processed into variable shapes and welded
- High porosity with excellent permeability, low-pressure drop
- Larger dirty holding capacity to help you save total cost
- Power Generation
- Chemical Processing
- Petroleum Refining
- Biopharmaceutical
- Food & Beverage
- High-temperature liquid or gas filtration
Filson: Your Premier Sintered Metal Filter Manufacturer
Filson sintered metal filters mainly consist of metal powder filters, sintered mesh filters, sintered metal fiber felt filters, and replacement sintered filter cartridges for other brands. No matter for any OEM specifications, Filsoncan create exact dimension filter and high filtration efficiency sintered raw material here for you at a competitive price.
Compare to other types of metal filter cartridges, Filson sintered filter cartridges have distinct advantages, such as being quite strong, durable, reusable, and mesh are not broken easily. If you want to have a long time using it and don’t want to replace a new one frequently, our sintered metal filters are your best choice.
Depending on your specific needs, we will design custom sintered metal filter elements for you, just please offer us below basic information: shape, applications, installation structure, flow rate, pressure drop, working pressure, working temp. and material, then our experienced engineers will offer you the proper solution for your reference and choice.
Sintered Stainless Steel Filter
Filson Sintered Stainless Steel Filters mainly include stainless steel sintered filter cartridge, sintered stainless steel plate, sintered stainless steel sheet, sintered stainless steel tube, sintered stainless steel filter disc. It is made of stainless steel 304 and 316.
Filson Sintered Stainless Steel Filters offer high filtering efficiency and long service life, widely applied in the filtration of liquid and gas. The filtering accuracy of ss sintered filter cartridges is available from 0.5 um to 300 um, with working temperatures from -200 °C to 1000 °C.
Production Processing of Sintered Wire Mesh
Filson Sintered Wire Mesh is produced by a series of technical processes, including rolling, pressurizing, and vacuum sintering. It has the average pore size and steady air permeability.
Firstly, woven wire mesh is uniformly rolled to make every layer in good contact, especially at the wire mesh cross points.
Then put one or more layers of rolled wire mesh inside a high-temperature furnace under mechanical pressure. This furnace is filled with specific inert gases. When the temperature reaches a point, “sintering” occurs and sintered wire mesh is formed.
Finally, we control cooling, the mesh now has good rigidity while wires and layers bond together. Some layers work as fine filtration, while others work for protecting and reinforcing.
By sintering multiple layers of different wire mesh, it is possible to custom your sintered metal filters with specific thickness, diameter, pore size, accuracy, and mechanical strength.
Filson Sintered Mesh Filters Classification
- Standard 5-layer Sintered Wire Mesh
- Sintered by Multiple Layers of Plain-woven Square Mesh.
- Sintered by Multiple Layers of Dutch-woven Square Mesh
- Sintered by Perforated Plate with Multi-Layer Stainless Steel Wire Mesh
Perforated Plate WithMulti-Layer Stainless Steel Wire Mesh
This Sintered Metal Filter is sintered by a standard SUS304 perforated plate together with multi-layers square woven wire mesh or Dutch woven wire mesh.
The strong and rigid perforated metal plate is for support while the woven wire mesh layers are used as the filtering layer. Due to the support of a perforated plate, this sintered stainless steel filter has a strong structure and mechanical strength.
Filson stainless steel wire mesh can be produced into various shapes, including sintered metal tubes, sintered stainless steel disc, and sintered stainless steel sheets. It is mainly reusable in food&beverage, water treatment, dust removal, pharmaceutical, chemical processing, etc.
Filson is proud to be among the top 10 factories to produce perforated plates with multi-layer stainless steel wire mesh with standards or custom dimensions.
People Also Ask
The simple definition of a sintered metal filter:
It is a filter that has undergone the process of sintering.
Sintering is a process of the metallurgy of your filter with different metals and alloys in powder form.
The process of metallurgy happens through diffusion at temperatures that are below the melting point.
Such metals and alloys that you can use include aluminum, copper, nickel, bronze, stainless steel, and titanium.
Sintered Metal Filter
You can use different processes to form the powder.
They include grinding, atomization, and chemical decomposition.
The advantages of having a sintered metal filter are just enormous.
I can assure you that you stand to gain a lot by using these filters on your application.
Among the various benefits that you can gain include the following.
Sintered Metal Filters
1. Corrosion resistance
What a sintered filter element offers for your application is a corrosion-free filter that will provide you with quality service.
Various reactions take place in your filter.
These reactions can either be chemical, mechanical, or physical reactions.
Such reactions can hurt the condition of your filter as well as the fluid that you are filtering.
However, by using a sintered filter element, you are sure that there will be no corrosion of the filter.
Also, you can be sure of the fluid that you are filtering won’t be affected by the filter element.
2. Better filtration
When filtering, you want to get the best out of your filtration which involves removing all the contaminants that are present in your fluid.
You can achieve this by using a sintered filter element for your filtration.
A sintered filter element offers quality filtration for your fluid with the results being fluid that is free of contaminants.
Adjusting the porosity of the filter element depending on the fluid means that you can achieve the perfect filtration that you want.
Since there will be no corrosion of your filter, no contaminants will be present in your fluid as a result of the reaction of the filter.
3. High thermal shock
The advantage of a sintered filter element is that it has a high thermal shock.
This is mainly an advantage when you are dealing with applications that have a high thermal shock.
During the manufacturing process bonding of various metals happens while maintaining the physical properties of the metals.
It is these physical characteristics of these metals that aid in absorbing the high thermal shock of your filter.
You can, therefore, use these filters in a wide range of applications depending on the thermal range of your application.
High thermal shock also ensures that you can filter your fluid efficiently without having to worry about the thermal heat of the application.
4. Reasonable pressure drop
If there is one aspect of your filtration that you need to ensure that is constant is the pressure of your fluid in your application.
That is precisely what a sintered metal filter offer.
A sintered metal filter can maintain the pressure of your fluid within your application thus ensuring maximum operation.
A slight drop in pressure might hurt your application.
Pressure vs Flow Rate
For instance, you may not be able to achieve the filtration that you want to due to there not being the relevant force to filter your fluid.
Also, drop-in pressure results in a drop in the fluid requirement of your application.
You will, therefore, find that your application may not get the fluid that it needs for your filtration.
5. Temperature and pressure resistance
You can easily maintain the temperature and pressure resistance of the individual metals.
This is because you can mix different metals by bonding without necessarily having to melt the metals.
The advantage of this is that the resulting sintered filter element has a high temperature and pressure resistance.
You can, therefore, use this filter in applications that have a higher temperature and pressure without having to worry about your filter element.
Among applications that have a higher temperature and pressure, resistance includes chemical reaction and gas treatment plants.
The use of sintered metal filters in such applications ensures that you obtain the best results for your filtration.
6. Tough and fracture resistant
Another benefit that you can get by using a sintered metal filter is that it is sturdy and resistant to fracture.
During the manufacturing process, the bonding of the metals takes place at temperatures that are way below the melting point.
The resulting product is a strong sintered metal filter that can withstand a variety of harsh environments.
For instance, you can use it in an application that regularly requires friction without having to worry about fracturing.
This is in contrast with other types of filters which can easily break or fracture when exposed to harsh environments.
7. Fine tolerance
Fine tolerance is another key benefit that you can obtain by using a sintered metal filter element on your application.
What fine tolerance means is the ability of your sintered metal filter to filter your fluid without any reaction to it.
This essentially means that once your filtration is complete, the sintered metal filter will still maintain its physical properties.
However, you need to ensure that the metal that you select for your filter does not react with the fluid that you are filtering.
This is because different metal reacts differently with different fluids hence you need to be keen.
8. A range of geometric possibilities
A sintering filter element allows you to enjoy a wide range of geometric options.
You can achieve this during the manufacturing process at process when you are inserting the powder into the dye.
The die is the one that is supposed to design your filter.
You are therefore at liberty to manipulate the design according to your specifications.
For instance, if you have a small filter that you want for your application, you can easily manipulate the design to have a smaller sintered metal filter.
Likewise, if you have an irregular design for your applications, you can easily design it in the die during manufacturing.
Let’s talk about the sintering process.
You may be wondering what is the concept of sintering all about.
That’s what this chapter aims to achieve to assist you in understanding the sintering process in the metal filter manufacturing process.
https://youtu.be/-K6_wbBnXmc
Keep reading.
i. What is Sintering?
The basic definition of sintering is the process through which the bonding of particles in powder form takes place.
The bonding takes place by diffusion in temperatures that are below the melting point.
In a micron range, a physical limitation does not exist between the metal powder particles as they were initially after the sintering process.
In essence, sintering offers shape- stability to high porosity materials.
It also provides a robust metallic component to the material.
The sintering process mechanically fixes the pores of these materials in regards to the position size.
ii. Sintered Metal Filter Manufacturing Process
The sintering metal filter manufacturing process basically involves three main steps.
The first steps include obtaining the powder form of your metal.
You can do this either through grinding, atomization, or chemical decomposition.
At this point, you can either combine this powder with another metal to form an alloy or use it as it is.
The benefit of sintering is that it allows the material to maintain its physical properties.
This process is so simple that there is no such alteration of the element.
Sintered Metal Filters
The second step involves pouring the powder into a die from where you can shape the design of your filter.
Forming the composition of the filter takes place under room temperature and high pressure.
The amount of pressure you can apply depends on the type of metal you are using since different metals have different malleable degrees.
While in the die, compacting of the metal powder takes place to form a solid filter.
Once this happens, you can go ahead and remove the screen, which is in a solid state, and subject it to a furnace under high heat.
Now, this is what we refer to as sintering.
During the sintering process, the metal particles fuse without having to melt.
This forms a high-strength, rigid and porous filter.
You can alter the porosity of the filter depending on the level of flow of either air or liquid that your screen will be filtering.
iii. Sintered Metal Filter Configurations
You can have different sintered metal filter designs that you can use depending on your application.
The choice of which design to use depends on the filtrate that you require.
Also, you can check on a filter design that minimizes either the backwash or the blowdown process as well as maximizing the throughput.
The important designs that you can select for your sintered metal filter include the following:
Filtration Modes
Outside-in Filtration
Outside-in Filtration design is where the filtration happens on the outer layer of the closed-end tubular filter element (LSP).
One of the ways of cleaning this kind of design is by using hydro- pulse backwash through the assistance of gas.
Outside- infiltration is useful in applications that offer a continuous flow of the fluid.
Since the cleaning is a thorough backwash, you can continue operating your application without having concerns about the contaminants.
Inside-out Filtration
In this design, the filtration of the fluid takes place on the inside of the closed-end tubular filter element (LSI).
Under this design, you can clean your filter using a variety of backwash modes.
These modes include empty shell slurry, full shell slurry, and empty housing wet cake discharging backwash.
You can find this mode ideal if you are using an application that has contaminants with low velocity.
This ensures that all the pollutants flow into the filter element.
There are several characteristics of inside-out filtration.
First, there is less heel, easier removal of contaminants as well as less heel.
As a result, the configuration of this type of filtration is quite easy if you compare it to outside- infiltration.
Secondly, you can select which filter element to use depending on the characteristics of the contaminants.
Attributes include the size and dimensions of the pollutants.
The advantage of this is that it offers you an optimum packing density.
Also, by using the filtrate outlet on the upper side, you are sure of removing all the contaminants along the length of the element.
Lastly, by using the outlet on the lower side, you have an assurance of displacing the filtered fluid from the filter using gas.
By doing this, you increase the filtration capacity of the liquid as well as maximizing on the contaminant removal.
Inside-out Multimode Filtration
Under this design, the filtration of your fluid takes place on the inside of the open-ended tubular filter element (LSX and LSM).
Sealing of the component takes place using two tub sheets meaning your fluid can either flow from the top or bottom of the inlet.
There are two ways that you can operate this design.
That is, as a light contaminant cleaning the filter with fluid filtration being the key.
You can also operate as a high contaminant recovery filter.
The multimodal cross-flow design allows you to operate continuously since there is a side outlet that will enable you to remove the contaminants.
You can also operate this design in batches by terminating the filtration process once it reaches the levels of the contaminants.
Once you are through with the filtration, you can clean the filter using the backwash process.
There are several advantages that you may gain from using this kind of sintered filter design.
First, it is highly preferred when there are highly specific gravity contaminants in the fluid.
The flow design usually is an upward flow mode in such scenarios.
Secondly, this design gives out the highest contaminant removal level and also you can conveniently wash the filter.
You also can operate the system either in crossflow mode or in the barrier.
Another advantage is that where the flow rate allows, you can use single vessel filters.
This will enable you to stop for backwash to occur or for maintenance purposes.
In cases where there is a continuous flow, you can use dual sintered filter systems.
This will allow for short offline periods for maintenance purposes to take place.
Lastly, for continuous operations, you can use the three sintered filter system.
One of the most sought-after answers is how a sintered metal filter works.
Most users find it a complicated task when in essence it is not
You may appear surprised by this but you shouldn’t.
Allow me to show you how this device works.
Take a look.
How Filters Work
Sintered metal filters are useful filters having two- dimensions where a collection of the contaminants takes place on the surface of your fluid.
While selecting the effective filtration grade for your liquid, you need to ensure that it balances the requirements of the application.
These requirements include:
- Contaminants retention
- Backwash ability
- Pressure drop
For this to happen, you need to consider a couple of factors.
Such factors include the fluid viscosity, the fluid velocity as it flows through the filter element, and the contaminant characteristics.
The aspects of the contaminant characteristics include the particle shape, density, and size.
If the contaminants are hard and have a regular shape forming dense cakes are suitable for surface filtration.
Sintered metal filtration depends on the increasing pressure drop to the point where the final pressure reaches.
It also depends on the constant flow of your fluid.
You can achieve the terminal condition by thickening the contaminants which increase to the point at which the fluid pressure drops.
This pressure keeps falling until it reaches the maximum drop for a given viscosity and flow requirement.
Backwashing of the filter takes place by pressurizing gas to the screen and opening the backwash discharge valve quickly as the backwash takes place.
The generation of a high reverse momentary differential pressure.
This effectively removes the contaminants from the element surface.
The reverse flow of the clean fluid through the filter element removes contaminants and directs them out of the filter.
A steady rise in the rate of pressure drop indicates that the size of the contaminant continually distributes evenly.
For consistent performance, you need to ensure that there is a steady pressure drop in the filter element.
If there is a change in the temperature of the fluid, it will affect the fluid’s viscosity.
As a result, there will be an increase in the pressure drop across the filter element.
You, therefore, need to maintain the operating temperature design of your filter during the filtration process.
When cleaning the filter, you need to adhere to the proper procedure of the backwash.
Obviously, at one point during the operations of your sintered metal filter, you will have t clean it up.
The process of cleaning up normally takes a few minutes if you pay attention to your manufacturer’s details.
However, there is nothing complex to worry about.
Here is how to go about cleaning your sintered metal filter.
Before cleaning your filter, you need to check the differential pressure of the sintered metal filter.
The starting process of cleaning your sintered metal filter is to place it in a nitrogen protection furnace and heat it to 380 ° C.
Sintered Screen
Leave it there for a period of 2 hours.
The efficient method of cleaning your sintered metal filter is ultrasonic cleaning.
This entails placing the filter in an ultrasonic machine and heating it for about 30 minutes.
However, you will still have to clean the porous parts of your filter, and this is where you need to take care of.
This is because there is a probability of contamination coming from the interior and contaminating the surface.
To clean these porous parts of your filter, you need to apply a method that will reach the interior parts.
As such, you need to ensure the continuous flow of the liquid to remove the contaminants.
Cleaning of the sintered metal filter becomes complicated especially when you are cleaning contaminants that are solid.
This is because these particles get trapped in the pores of the filter.
To solve this, you need to direct the flow of the fluid in the opposite direction from the direction that which the particles got stuck.
This is what is commonly known as backwashing.
If this proves hard, you can still remove the contaminants by dipping the filter multiple times in a fluid.
While doing this, you allow the contaminant in the fluid to absorb the fluid.
After it absorbs, you can let it drain for a few minutes then repeat the process a couple of times.
You can then use a vacuum hose to remove the contaminants from the sintered metal filter.
Of importance is to ensure that while cleaning the sintered metal filter you take the necessary precautions.
This includes ensuring that the components of the filter don’t break up or disintegrate.
There are different types of sintered metal filters that you can find in the market.
However, the choice of which one to use depends on your application.
To enable you to make the right choice when choosing a sintered metal filter, here is a look at the common types available in the market.
i. Sintered Porous Metal Filter Elements
Sintered porous metal filters elements are filters that have pores for filtration purposes.
These filters typically have high mechanical and pressure tolerance.
The process of making a sintered porous metal filter is a complex process.
However, what happens is that there is the sintering of the plastic using a high molecular mass thermo polymer powder.
During this process, you need to pay special attention to the cryogenic ground powder.
This provides the filter with a particle retention range of between 5- 200 microns.
These porous can have as high as 70% pressure drop elements.
This depends on the size of the pores as well as the filtration characteristics of your filter.
The usage of these filters is common in an application where the temperature is below 80 degrees Celsius.
ii. Pleated Sintered Metal Filter
The pleated sintered metal filter is a kind of filter that uses pleats for the filtration of your fluid.
The advantage of these filters is that they have a large filtering surface area when you compare them with the porous type.
Also, these filters are corrosion-free, and you can quickly clean them.
The process of manufacturing this filter involves the use of individual components.
What happens is that there is a combination of these different components in a cylindrical shape.
This forms an external surface that has several slots with the width defining the pore size of your filter.
The housing of the filter is in a cylindrical position which allows the pleats to hold together.
This allows for the fluid to flow through the pleats towards the pipe that collects the filtrate.
Extraction of the contaminants is through a precise dimension which you can determine using the slot width.
To be honest, only the best quality sintered metal filter can work for your application and achieve the results that you want.
However, to be able to pick the best quality sintered metal filter for your application, you need to be vast with their features.
Sintered Metal Filters
Here is an in-depth look at these features.
Physical durability
Physical durability is one of the features of the sintered filter element that you can take advantage of.
The physical strength comes about as a result of the bonding of different metals during the manufacturing process.
Since there is no melting of these metals, they can maintain their physical properties.
It is these physical properties that can offer durability to your sintered filter.
The advantage of this is that your filter can offer quality service for a longer duration without the necessity of replacement.
Durability also implies that you can gain value for your sintered filter on your application.
Temperature resistance
To achieve the best of your filtration, you need a filter that can withstand the temperature of your application.
That is what a sintered metal filter offers for your use.
By choosing a metal that has a high-temperature resistance capability, you can have a sintered filter that fits your application.
The critical thing to note is that sintered metal filters are a product of different metals.
As such, when selecting a sintered metal filter, you need to ensure that the metal has the temperature resistance as your application.
Choosing any sintered metal filter may cause your filter to fail especially if the temperature range is lower than your application.
Corrosion resistance
Many filters fail to achieve the desired level of filtration with time due to corrosion of the screen.
The filter element corrosion occurs when there is a reaction between your filter and either the environment or the fluid that passes through.
Corrosion may be a result of either chemical or physical reaction between your filter and the external factor.
As a result, there is your filter gets “eaten away” which in turn reduces its efficiency.
However, that is not the case with a sintered metal filter.
No reaction takes place between your filter and the external factor which in turn makes it hard for the filter to be “eaten away.”
This ensures that your filtration is as effective and as efficient as possible.
Precise filtration
You can obtain the filtration that you desire with a sintered filter.
This is due to the availability of the pores in the element.
The ability to adjust the porous material during filtration makes it quite easy to achieve the level of filtration that you want.
That means that if you want finer filtration, you can easily select a sintered metal filter with tiny pores.
Likewise, if you want average filtration, you can select a sintered metal filter with average pores.
High-quality material
One of the features that you look for when selecting a filter is quality.
Getting a filter that will offer you the best service for a long duration is very vital to your filtration.
The advantage of a sintered metal filter is that you have the highest quality material to select from when purchasing a filter.
The reason for this is that the bonding of different metals ensures that you obtain high-quality metal for your sintered metal filter.
You can have different sintered metal elements which are a result of different bonding metals.
The result is of a higher quality as a result of maintaining the individual properties of the metals.
Varying filtration grade from 0.1 microns to 100 microns
The fact that you can customize your sintered metal filter gives you the advantage of achieving the result that you want.
For instance, you have a wide range of filtration range to select when you are designing your filter.
Filter Beta Ratios – Photo Courtesy: Advanced Fluid Systems
You can select from as low as 0.1 microns to as high as 100 microns of the filtration grade that you want your filter to be.
This, of course, depends on the level of filtration that you want to achieve.
If you want to achieve finer filtration, you will select a smaller filtration grade for your application.
Custom pore sizes and flow characteristics
With a sintered metal filter, you are at liberty to customize the pore sizes and the flow characteristics to suit your application.
That is to say; if you want a tiny or large pore size for your filter, you can quickly achieve it using a sintered metal filter.
This is thanks to the ability to control the porosity of the sintered metal filter during the manufacturing process.
Also, you can easily customize the flow of the fluid on your screen to match that of your application.
If the flow of your application is from the bottom to the top or from right to left, you can quickly change your sintered metal filter to correspond with it.
Fully welded sintered metal filter element
During the manufacturing process, you can weld most parts of the sintered metal filter together.
This gives a much more stable filter than screwing the components together.
Screwing can make these components fall apart in an application that has high vibrations.
The disadvantage of this is that you will continuously be maintaining your filter.
This may result in a loss of productivity of your application.
However, you can minimize all these by using a sintered metal filter.
The welding of these filters allows for little movements of the components thereby ensuring maximum productivity of your application.
Dirt holding capacity
One of the main features of a sintered metal filter that you will find crucial is the ability to hold the contaminants.
Contaminants holding capacity is essential since it will determine how long you can continue operating without stopping.
You can have different sintered metal filters that have different dirt holding capacities.
The choice of which sintered metal filter to pick depends on the application that you are using.
Large applications need a high dirt holding capacity filter whereas if you have a small application, a smaller capacity filter will do.
Type of sintered metal filter material
Another feature that is very common with sintered metal filters is that you can select the metal you want.
We have seen the sintering process is all about the bonding of different metals either individually or as alloys.
The resulting product is a durable and efficient filter that you can use.
This, therefore, means that you are at liberty to select the right metal that you can use for sintering your filter.
Among the considerations to make when selecting a metal for your sintered metal filter is the application that you are going to use.
The metal needs to withstand the conditions of the application for it to be effective.
High permeability
Permeability refers to the pressure drop measurement of a given fluid at a given flow in a filtration unit area.
High permeability is one of the characteristics of a sintered metal filter that makes it adaptable to its function.
For efficient filtration to occur, there is a need for a high-pressure drop which this feature makes it possible for the sintered filter to have.
The pressure drop needs to be in line with the maximum temperature of your fluid for efficient filtration to take place.
Different sintered metal filters have different permeability levels that you can select depending on the fluid that you are filtering.
Sintered Metal Filter Pressure Drop
An attractive feature of a sintered filter metal is its ability to maintain the pressure of the fluid of your application.
The advantage of this is that you can completely filter your fluid.
What happens when the pressure drops are that there is a lack of enough force to allow for the fluid to pass through the filter.
As a result, you will find the filtration of your fluid not complete since there will still be the presence of contaminants.
Also, you will find that your application may not be able to achieve the fluid requirement that it needs.
However, the use of a sintered metal filter helps to prevent all this from occurring.
Quality of sintered metal filter disc
There is no doubt on the quality of a sintered metal filter more so the filter disc.
The manufacturing process ensures that you only obtain the best of your sintered metal filter.
The filter disc, in particular, is an important component of your filter.
It is here that the pressure builds up as filtration takes place.
You, therefore, need to ensure that this disc is strong enough to withstand this pressure.
Different filter disc always breaks after some use due to this pressure.
However, the sintered metal filter disc is strong enough to withstand the pressure of fluid for a long duration.
This ensures efficiency during the filtration process.
Sintered Metal Filter Cartridge
The sintered metal filter cartridge is the most important part of your filter.
It is here where the actual filtration takes place.
As such, sintered metal filter cartridge ensures that you have the best filtration of your fluid.
The durability of this cartridge ensures that you get value for money when you are using them.
So, which application can you use your sintered metal filter apart from the one you already have?
The truth is that you can find extensive use of these filters in different industries.
Different sizes of Sintered Metal Filters – Photo Courtesy: PAULGOTHE
Among the common applications include the following.
Chemical Processing
You can find the application of the sintered metal filter in the chemical processing industries.
Such industries include the nuclear manufacturing industry.
Several characteristics make sintered metal filters advantageous in chemical processing industries.
They include corrosion-resistant, high-temperature resistance it does not react with the chemicals.
Petroleum Refining
For petroleum refining, you can use a sintered metal filter element to filter the different fuels effectively.
Depending on the degree levels, you need to ensure that you have entirely filtered a particular fuel from the rest.
A sintered metal filter can help you achieve this.
Among the characteristics that can make this filter useful in petroleum refining include its chemical non-reaction with the fuel.
Filtration will, therefore, be of that particular fuel that is free of all contaminants.
Also, you can use it in high temperatures which is a common thing in petroleum refining.
Power Generation
Power generation especially hydroelectricity requires the continuous running of the turbines.
The working environment of the turbines frequently needs filtration.
Shutting down your turbines means that there will not be power generation.
To ensure effectiveness and efficiency in power generation, you can use sintered metal filters.
These filters are useful in power generation by allowing filtration of the water in the turbines.
They don’t corrode with the water meaning that you can use them for a long time.
Gas production
Another area of application for the sintered metal filter is in the production of various gases.
The sintered metal filter is useful since they don’t react with the gases and the fact that you can use them in a different environment.
Food and beverage
In the food and beverage industries, the application of this filter is in the extraction of essential nutrients and juices.
Filtration takes place to prevent these nutrients from washing away during the processing period.
The advantage of these filters is that they do not react with the particular food or beverage.
While using these filters, you have the assurance of the quality of your process.
Sintered Metal Filter Assembly
Also, they offer quality services for an extended period which ensures that you get value for your money.
Filson specializes in the manufacturing and customization of various sintered metal filters.
Having been in the industry for over 15 years, we have grown to understand the multiple needs of our customers.
Our clients prefer our sintered metal filters due to their proven durability, temperature resistance, precision filtration characteristics.
Our sintered metal filters are also corrosion resistant.
We offer our sintered metal filters in different alloys such as titanium, nickel, and stainless steel.
These alloys come in different media grades from as low as 0.1 microns to 100 microns ensuring that you meet your needs.
In case you want to customize your sintered metal filter, we will work with you to manufacture one that meets your expectation.
This includes sticking to the design of your sintered metal filter as we adhere to international standards.
Get in touch with us today and let us develop a sintered metal filter for your application.
Conclusion
As it turns out, sintered metal filters have a wide range of applications that you can use.
However, the trick is in choosing the right sintered metal filter.
You need to understand the different characteristics of quality of these filters so that you can choose the filter that works best for your application.
Finally, although there are different manufacturers and suppliers in the market, there is still a need to be cautious during selecting.
But if you have limited options, you can choose Filson manufacturer to provide you with sinteted metal filters.
Now you have mastered all the knowledge needed to choose high quality sintered metal filters.