Your Trustworthy Well Screen Manufacturing Expert In China
When you need to successfully finish an environmental drilling job, Filson water well screen is an irreplaceable choice. It can efficiently prevent the unneeded sands from entering the well, while achieving higher productive efficiency and longer using life of the well.
Filson has a team of specialist engineers and experienced workers to faultlessly assist your water well screen project. Additionally, our advanced well screen production line can also serve your urgent or large quantity order within 7-15days.
Well Screen
Why our customers choose Filson well screen?
- More Than 18 Years Experience
Filson has over 18 years of experience in manufacturing well screens, with our specialized engineers, skilled workers and advanced production equipment.
- Short Delivery Time
Filson owns a series of a complete production lines to fabricate water well screens, thus can ensure the fastest production period and the shortest delivery time.
- OEM Service
Filson always provides customized service with a wide range of materials, slot sizes, lengths, diameters of well screens. We will assist you to design the most perfect solution for your special needs.
- Flexible Design Ideas
Filson devotes to produce well screens with flexible design ideas and innovative technology, making your filtration business completed successfully.
- Wonderful Attitude
No matter you are a new customer or an existing customer, Filson will help you solve your well screen doubts with 200% enthusiasm and patience.
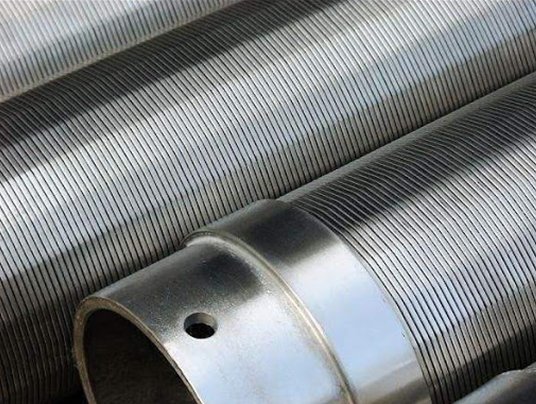
Filson: The Optimal Well Screen Supplier With New Innovations And Technologies
Filson well screen, also known as water well screen, is an essential filter media used for well filtration applications. It allows water to enter the pipe from several entry points while preventing the unwanted contaminants, to achieve the filtration purpose.
Filson water well screen is commonly made of 304, 316L, or 904 stainless steels with high mechanical strength, withstanding the pressure from formation and borehole. Of course, other corrosion-resistant alloys are available upon your request.
Filson well screen is manufactured with a continuous v-shaped slot to reduce the entrance velocity of water and encrustation rates. Besides, Filson well screen has a large surface area without clogging, thus provide superior filtration performance.
Well screen slot size selection is a critical step, typically based on the particle size analysis of the formation sample. With the standard slot size range from 0.005” to 0.5”, Filson well screen can control sand particles and silt from the well perfectly.
For different wells and aquifers, Filson well screen may be constructed with a variety of different materials and designs. Typical water well screen types include stainless steel well screen, PVC water well screen, gravel packed well screen, continuous slot well screen.
Compared with other screen design like horizontal louver screen and bridge slot screen, Filson wedge wire well screen has higher open area to get lower head loss, and can be used in wider applications.
Moreover, well screen manufactured by Filson supports to add a gravel pack to improve its filtration efficiency. The purpose of well screen and gravel packs is to maintain open access within the aquifer and ensure the well development is not impeded by sand.
After a period of using, your water well screen may be damaged, whereas a well screen replacement is not feasible, you can install a smaller diameter screen inside the original well screen. This will even out the water flow thus reduce the sand entering.
As one of the most professional water well screen suppliers, Filson has more than 18 years of design and production experience. We will always be your business partner in well screen field, helping you select the best water well screen or design your personalized one.
Just give us your specific application, well conditions and formation properties, we can guarantee to customize the most suitable well screen for you.
Interested in other filtration media? Filson supplies numerous types of filters: wire mesh filter, sintered metal filter, wedge wire filter, stainless steel basket filter… Each Filson filter product are manufactured with the highest quality standards and certificated ISO 9001.
Contact Filson today! Call at +86 157 3695 8886 or email to sales@filsonfilters.com as you like!
Filson Well Screen Benefits:
- High mechanical strength to withstand installation and borehole pressures
- Superior corrosion resistance to ensure working well in groundwater
- Various slot size selection for giving optimum open area
- Easy to clean and backwash to obtain long service life
- Large surface area with low pressure drop
- Less pump wear thanks to proper sand preventing design
- Difficult to clog since its wedge wire construction
Filson Well Screen Specifications:
- Raw material: stainless steel, galvanized steel, low carbon steel, PVC, other alloys
- Slot size: 0.005-0.5 in.
- Length: up to 5800 mm
- Outer diameter: 1.7-35.9 in.
- Inner diameter: 1.1-34.3 in.
- Screen thickness: 1.5-10 mm
Note: Length of continuous slot well screen can up to 40 ft.
Filson Well Screen Applications:
- Water wells
- Geothermal systems
- Recharge wells
- Monitoring boreholes
- Deep well dewatering
- Pressure relief wells
- Aquifer storage & recovery wells
- Irrigation systems
People Also Ask
A Well Screen is one of the filtering devices used in the wells as an intake portion in confined or unconfined aquifers.
With the help of this screen the water from surroundings of well can enter into the well.
That is, without causing dirt, silt, or debris from entering the well.
Besides, it structurally supports the aquifer material.
Well Screen
Silt or debris may cause excessive abrasion and early failure of the water well machine, as well as plugging of home appliances.
Furthermore, sand can build up in a well and block off water-bearing zones.
A Well Screen has several holes.
It is placed in the aquifer layer.
Thereby, allowing water to enter the well.
The water well screen is placed on the bottom of the water-bearing, expanding upward from there.
It is not an easy task to dig a water well that depth with standard equipment. So the screen is installed as deeply into the surface as possible.
Six to seven meters underneath the groundwater is deep enough to obtain sufficient yearly yield.
It will vary depending on the various factors that are difficult to predict, such as aquifer conductivity and surface recharge.
It should be strong enough to withstand pressure and stress.
Position Of Well Screen
Many ground domestic wells do not require a Well Screen.
Water Well screens are not a one-size-fits-all item.
If one is required, local water well contractors understand how to select a screen and determine the appropriate screen length.
A screen length of 4 to 5 feet is usually sufficient for most domestic wells.
Different types of water well screens are:
- Continuous-Slot Screen
- Slotted Plastic Screen
- Bridge Slot Screen
- Wedge Wire Screen
- Hub and Header Lateral
Continuous-Slot Screen:
A continuous-slot screen is also named a wire wrap screen.
The continuous-slot screen is widely used for water, oil, and gas wells worldwide.
It is the most common screen type in the water well industry.
It is made by winding triangular-sectioned rolled wire around a circular array of longitudinal rods.
Welding is used to connect the wire to the rods. Welded screens are made up of stainless steel.
Continuous Screen for water well
Slot openings are formed by spacing successive turns of the outer wire apart to achieve the desired slot size.
Slot openings have been marked with numbers that correspond to their width in thousandths of an inch.
Slotted Plastic Water Well Screen:
The slotted plastic water well screen is particularly used in soils enriched with clay where no aquifer zone can be observed.
Slotted plastic screens are resistant to corrosive water, are simple to install, and are reasonably priced.
The open area of slotted plastic screens is less than half that of continuous-slot screens.
Furthermore, plastic pipe materials are 1/6 to 1/10 the strength of stainless steel well screens.
Slotted Plastic Screen
Bridge Slot Screen:
This type of water screen has bridge openings that are spaced and aligned in rows, enhancing the positive effect and strength of the screen.
Its slots are usually placed onto a flat sheet.
It results in a spiral-style bridge slot with a good style and a unique structure, providing compression resistance.
It can be galvanized, stainless steel, or made of anti-corrosive material.
Bridge Slot Screen For Water Well
Wedge Wire Slot Screen:
Wedge slot screen has similar characteristics to wire wrapped water well screen.
It is manufactured from stainless steel or minimal galvanized steel.
Wedge Wire Screen
Hub And Header Lateral:
It uses an even distribution with low-pressure concentrations, and each of the header laterals is made up of screen laterals connected to the main header.
It allows for a uniform flow of treatment media within a vessel.
In addition, the header laterals can also transfer or receive inflow. And its placement within the vessel determines this.
Hub and Header Lateral Screen
Additionally, the systems can help side, center, top, and bottom entrance piping. Stainless steel is used in making of hub and header lateral.
Continuous-slot screens have the greatest intake area per unit area of screen surface than any other type of screen.
This type of screen has the most open space.
Groundwater is an important part of our ecosystem. When it is invaded, it decreases the level of water. A lack of water can also lead to increase consumption of energy.
This screen protector prevents sand from entering the screen and reduces friction on the pump.
For greatest well efficiency, the percentage of open area in a screen should be equal to or greater than the aquifer material’s average porosity.
Compared to a screen with a limited open area, water flows freely through a large intake area like in a continuous-slot screen.
Advantages Of Continuous Slot Water Well Screen
- The possibility of particles becoming stuck in the bridge screen is the best characteristic of the bridge screen.
Because of the slot’s unique feature, it has a higher capacity for cleanliness.
- You can easily install and uninstall the screen.
- You can make it from a variety of materials. It adapts to a wide range of environmental conditions.
- It is more long-lasting because it resists deformation, compaction, and tensile stress.
- It has many screen connection methods that make it easy to use.
Benefits Of Bridge Slot Screen
There are various methods for installing water well screens.
Though certain procedures may be more practical or cost-effective in certain areas or when specific drilling rigs are used.
The nature of the aquifer materials determines the exact procedures to be followed when installing a water well screen.
Others factors include the drilling method used, the borehole dimension, the hydraulic conditions in the aquifer, and the casing and screen material.
You can use these given methods to install Well Screen:
- Pull-Back Method
- Single String Installation Method
- Washdown Method
Installation Of Well Screen
The pull-back method of water well screen installation is safe.
It reduces problems caused by heaving sediments, sloughing borehole walls, and setting the screen at an improper depth.
This method also allows the screen to be removed and replaced if necessary without causing any disruption to the sanitary grout seal outside the water well casing.
Steps Involved In The Pull-Back Method:
- Install the casing to the full depth of the well
- Lowering (telescoping) the water well screen inside the casing
- The casing is then pulled back or lifted far enough to expose the screen to the water-bearing formations.
The casing must be firm enough to be set down the well and then pulled back the length of the screen.
Some contractors attach a rising pipe (blank) to the upper end of the screen to expose the entire screen without slipping out of the casing.
On the upper side of the screen, a neoprene packer is installed to provide a stand-tight seal.
Two or more packers are used in series to eliminate problems caused by minor deviations in casing or packer dimensions caused by improper handling.
Pull-Back Installation Method
The screen is present in almost every well to prevent materials from passing through the wells.
On the other hand, these screens accumulate sediments from water that passes through them, gradually lowering your water pressure until it’s completely clogged.
To avoid this situation, use a chemical application to reach the screen down in the well and dissolve the deposits.
This allows water to flow normally again.
Steps To Clean The Screen:
You can use the following steps to clean the water well screen:
- Locate the well’s priming plug port, which is located before the pump inlet.
- Pour granular acids such as phosphoric or sulfamic acid down the port opening.
- It allows the acid to reach the water well screen, where the granules will slowly dissolve and react with the build-up without releasing large amounts of chemicals all at once.
- There is no need for a large quantity of acid typically; a small amount of acid is sufficient.
- Allow the chemical to do its work. It is a slow-release product, and it may take several hours or more.
Cleaning Of Water Well Screen
A water well screen is figured to be suitable for allowing sufficient sand-free water flow into the well. It causes the least amount of hydraulic flow.
The best-designed water well screen should include the following features:
- It must have closed slot opening holes to provide a uniform distribution of open areas.
- It should have a maximum open area.
- It should have V-shaped slot openings that widen inwardly.
- It should have the property of corrosion resistance.
- It should be strong enough to withstand the external forces that the screen may encounter during and after installation.
- Tapered slots screens are hydraulically efficient and possess self-cleaning properties.
Design Of Well Screen
The screen’s length is also important in the design of the screen.
A water well screen that is too short affects well efficiency.
In contrast, a water well screen that is too long has issues such as cascading water, accelerated corrosion or incrustation, and entrained air.
The thickness of the aquifer, available drawdown, and categorization of the aquifer all influence the optimal length of the water well screen.
Choose a size that keeps the sand at bay while allowing water to flow freely into the well.
It is one of the types of screen developed many years ago for use in wells.
Originally, shutter screens were made by punching downward-facing louver apertures into short lengths of the pope.
Then welding them together to form sections up to 20 feet long.
Now, there’s a way to make tubes that can have a length of 50 feet. If you use mandrel internally and die blocks externally, you can perforate the material.
Shutter Well Screen
The versatility of shutter screens makes them a cost-effective choice for meeting specific customer needs.
They come in a different form of patterns and you can customize them to fit any need.
You might need to use lower velocity screens. These are available in the market, which makes it easier for you to keep the head loss down.
Well, a louver aperture having a downward face is a great option for wells having gravel envelope. It has a lot of benefits, which include its security and ventilation.
There are various benefits of the shutter well screen.
- A shutter screen is an important part of many structures because of its high collapsing strength. It has more collapse power than an empty casing.
- As with wire-wrap screens, its resistance to collapse does not vary with aperture size.
- In shutter screens, tight swabbing can be used without danger to develop and redevelop wells. This is because of extra mechanical strength.
- Down-the-hole cameras, model studies, and years of experience all show that the louver-shaped opening resists clogging better than any other type of screen.
- In other words, when installed properly, the down orifice on a shutter screen provides a more controlled release of gravel so that it does not fall everywhere.
Rotary Swab
The difference between slotted pipe screen and perforated pipe screen are:
Slotted Pipe Screen | Perforated Pipe Screen |
Slotted pipe screens are manufactured by making machine-cut slots into steel or plastic casing at predefined distances. | A perforated pipe screen is a length of the casing with holes or slots drilled or cut into it. |
The slotted pipe screen has a smaller open area than any other slot screen. | This type of screen is generally inefficient and should not be used in sand and gravel aquifers. |
These slotted pipe screens have an ordinary efficiency. | Perforated pipe screens may be useful in semi-consolidated aquifers. |
The water well screens come in PVC or stainless steel forms. They have a major role in the finishing of the well.
Some basic factors to remember when selecting a water well screen are as follows:
- Must stop the gravel and other debris.
- Should be industrially reliable. (Screen sizes are in 0.005-inch increments)
- It should be compliant to development (allow for a two-way flow)
- It should have the capability of producing sand-free wells with a concentration of less than two ppm.
- Must check the type of screen. It comes in PVC and stainless steel forms.
- The length of the water well screen should not be greater than the thickness of thin aquifers.
- Make sure to inspect the diameter you are choosing your well screen.
PVC Well Screen
You should know the role of slot size in water well manufacturing.
When possible, select a screen slot size that corresponds to the aquifer’s range or grain size.
The interaction of sand and gravel has a significant impact on the formation around the screen.
Small openings limit water well yield.
Furthermore, small slot sizes cause high velocity in the water passing through the screen. Scale or incrustation forms on the screen over time.
If the openings are too large, you may need to develop the well more than usual, or you may be unable to clear the well of sand.
Screen slots sized to retain the coarsest one-third to one-half of the aquifer’s sand or gravel work best in a naturally developed well.
The slots should allow about two-thirds of the sand in the layer behind the screen to pass through.
A screen that covers coarse and fine strata may require sections with varying slot sizes.
If you artificially pack the screen with gravel, make sure the slot openings correspond to the size of the gravel you use.
Screen openings that retain approximately nine-tenths of the gravel perform the best.
Slot Size Of Water Well Screen
Single String Method:
The casing and screen are installed as a single assembly by using this method. To install assembly, follow the steps below:
STEP 1:
Attach couplings to the casing and screen section’s top. Attach a sand trap to the string’s bottom.
STEP 2:
After inserting the entire string into the borehole, use casing elevators to carry almost all of the string’s weight until the formation collapses around the screen.
STEP 3:
Insert the drill pipe into the casing until it reaches the bottom of the screen, and then pump water into the well to displace the drilling fluid.
STEP 4:
Raise and lower the drill pipe to clean the entire length of the screen.
STEP 5:
Allow the formation to form around the water well screen. Continue with the completion and development of the well.
The Disadvantage Of The Single-string Method:
The weight of a long string of casing on top of the screen is a disadvantage of the single-string method.
When the screen reaches the bottom, it becomes a loaded column prone to buckling due to its slenderness.
When the screen has reached the proper depth, you can prevent buckling by supporting it on casing elevators.
This is until the formation material collapses around it and supports it laterally.
Single String Method
Washdown Installation Method:
The washdown method involves the following steps:
STEP 1:
Connect the wash pipe to the kelly and turn on the mud pump. Water (not drilling mud) should circulate down the wash pipe.
STEP 2:
Allow the screen to move down as the material washes and the circulation continues. Take measurements and stop the screen’s descent when the packer is near the bottom of the casing.
STEP 3:
Turn off the pump and allow the aquifer to fill in around the screen.
STEP 4:
Once the wash pipe is clear, add more water. Raise and lower the string several times until the lower end of the string travels the entire length of the screen. More drilling mud and fine sand will wash out of the formation due to this action.
STEP 5:
Proceed with the development process. Remove the wash pipe and move ahead with the development work.
The basic purposes of water well screen are:
- A water well screen is a filtering device that connects to the bottom length of the casing. It allows water to flow into the well while keeping most sand and gravel out.
- A water well screen is important in all wells that are completed in an unconsolidated aquifer.
- Screened water wells generate more water, last longer than unscreened wells, have fewer problems, and are easier to clean out than unscreened wells.
- The screen and gravel pack should, first and primarily, prevent the well from collapsing.
This is due to the abstraction of large amounts of sand and, secondly, damage to the pumps due to sand particles in the water.
You should use the screen for better working of the water well.
Water Well Screen
The main purpose of filter pack in water well screen is:
Many water wells are designed to support a filter pack, which alters the screen installation process.
Filter-packed wells differ from naturally developed wells in that a predetermined thickness of silica sand is placed around the water well screen.
The use of a filter pack is determined by the geologic conditions, drilling methods, and type of screen.
The filter pack helps to filter the screen while also stabilizing it.
The primary goal of filter-packing is to introduce more porous material than the native formation into the area immediately surrounding the water well screen.
The benefits of filter-packing a water well include:
- Increased porosity
- Increased hydraulic conductivity
- Increased yield
- Decreased entrance velocity
- Lowered sand pumping and simplified grouting.
To ensure that the contaminants are not introduced into the well during the filter-packing process, the filter pack must be chlorinated.
This is before being placed in the open annulus.
All environmental drilling jobs must include the installation of a water well screen.
It is essential to install a screen in all the wells.
It helps to extend the life of the well and keeps the water flowing readily.
Unconsolidated materials, such as sand and fine silt, can easily flow with water.
It is necessary to remove these fine particulates before the usage of water.
A water well screen aids in keeping the majority of this fine material out of your well water.
It reduces the need for filtering and keeps the water flowing.
During installation, add a gravel pack around the water well screen. It aids in filtering the water even more than the water well screen alone.
Around the screen, the gravel pack adds another layer of filtering. It also serves as a structural element, aiding in the retention of surrounding materials.
Installation Of Well Screen
The following steps will help you in the preparation water well screen:
Identify The Function Of The Water Well Screen:
The water well screen is essential: it connects to the bottom of the long PVC water well pipe and allows water to enter while filtering out all the debris and sand.
The water well screen comprises hundreds of small slits that filter out debris and keep your water clean.
Take Notice Of The Water Well Screen Pattern:
There will be a 4 inch (10.2 cm) gap with no slits between the bottom of the 8 inches (20.3cm) PVC pipe.
This 4 inches (10.2 cm) space will connect to the PVC pipe.
Start Making Your First Slits:
Make three circular slits. The distance between each slit should be about 1.4 inches (3.5 cm).
Make completely sure your slit does not extend around the pipe. Keep a small gap between every slit’s ends.
Make One More Set Of Silts:
Make three more slits two inches above the first set. Make sure that the slits do not wrap around the screen, but instead, keep a two-inch gap between the ends of the slits.
Continue To Make A Slits:
Continue designing sets of three slits two inches apart. When the screen reaches 6 feet (1.8 m) in length, you can stop.
Cut Out The Slits:
Cut slits by using a saw. Saw each line carefully; make sure not to cut through the pipe. Continue saw until you’ve cut a slit in each line.
Some other steps are:
- Locate a water well screencap
- Use a primer coat to the water well screen
- Use pipe cement on the primed pieces
- Place the screen’s end cap on top of the water well screen.
Additional Resources:
For any questions or inquiry about well screens, contact us now.