Demister Filter Fabrication
Filson is a professional manufacturer of extremely high quality demister filter in China. We can provide various sizes and types of demister filters.
- Easy to install in all process equipment
- Most cost-effective solution when equipment sizes are set by other requirements
- High efficiency with low pressure drop
- Emergency delivery available
What is Demister Filter
Filson demister filter, also called demister mist eliminator, serves to gas entrained mist separation columns to ensure the filtration efficiency. As the entrained liquid gas stream flows through the mesh of demister filter, liquid will collect as droplets.
Filson demister filter is usually used for removal of contaminants, for example chromic acid mist, alkaline mist, electrolytic nickel mist, sulfuric acid mist, phosphoric acid mist, chromium anodizing, sulfuric acid from battery charging operation, alkaline cleaning, etc.
And Filson demister filter is extensively available for industrial and chemical applications with high liquid/droplet separation efficiency and low pressure drop. It is a motionless, embedded device that in most cases is installed in evaporators, scrubbers, pressure vessels, etc.
Demister Filter Series
Filson demister separators, also named droplet separators, are available in a variety of vertical and horizontal droplet separators. Usually choose the vertical type because its efficiency does not vary with liquid level.
Filson demister pad in vessel is used to ensure the filtration efficiency and prevent product loss and equipment damage. Its filtration fineness can reach 3μm to 5μm.
Filson demister filter element is at the core of every Filson Demister Filter. It has a full range of element for almost any application, size, filtration efficiency and dirt holding capacity.
Filson demister plate provides a large contact area for high filtration and separation efficiency in the chemical, petroleum, and pharmaceutical industries.
Filson demister mesh is a high efficient gas-liquid separation device. It can achieve high collection efficiency up to 99% at velocities of 1-8 m/sec.
Filson air demister is very effective in removing particles below 2 microns. Even for particles smaller than 1 micron, its efficiency of this demister is up to 99.99%.
Demister Filter Advantages
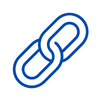
Filson demister filter is made of corrosion resistant material such as PVC, PP and stainless steel. Therefore, it has long service life.

Filson demister filter is equipped with complete rigid support grid, allowing direct mounting on suitable support elements. It adopts sectional installation, easy handling and disassemble.
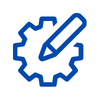
We can supply demister filter with the appropriate filtration accuracy for your needs. And Filson demister filter has a wide range of sizes and materials.
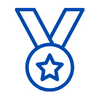
Filson demister filter achieves to 99% separation efficiency for particles below 5 micron with pressure drop around 25 mm WC.
Main Types of Demister Filter
Filson demister filter is available in four alternative types to suit your specific size of entrained material removal, including mesh, vane, cyclone and fiber-bed types.
- Wire mesh demister is the most commonly used method to remove entrained droplets down to 3 mm in diameter from air streams with velocities greater than 1 ft/sec.
- Fiber-bed demister filter is effective for large liquid flow rates and for removing droplets less than 3 mm in diameter. However, fiber bed is limited to gas flow rates of 3 to 10 m/min, and it causes high pressure drops.
- Vane-type or cyclone demister filter is only effective for droplets larger than 3 microns in diameter and at velocities greater than 500 feet per minute.
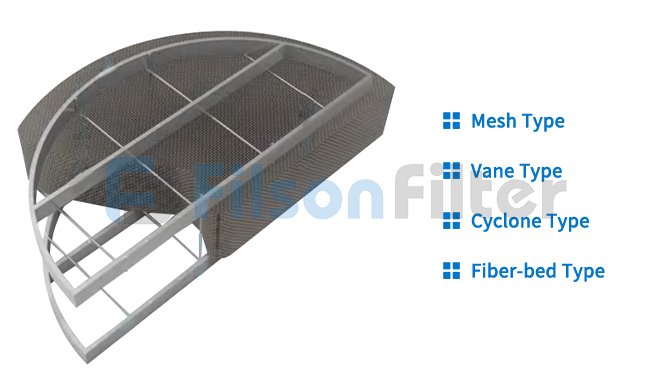
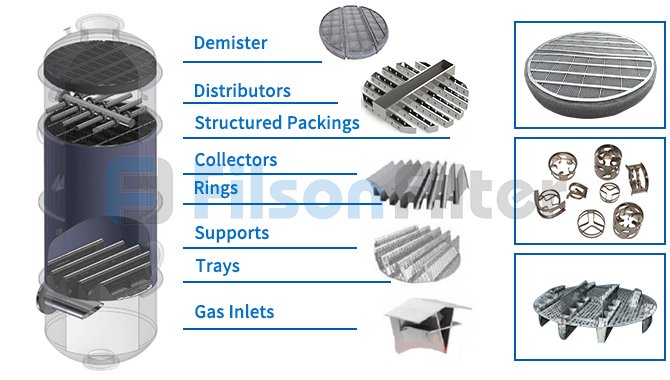
Demister Filter Function:
Filson demister filter are used to filter the gas and separate the liquid droplets from the flowing gas medium. During droplet separation, droplets flow through the wire mesh with inertia causing them to hit the surface of the wire and then collect at intersections in the wire mesh. The accumulated droplets then form larger droplets and move downward and are collected at the bottom.
- Prevent contamination of the process
- Protect downstream equipment to reduce damage or corrosion
- Recover useful product and increase product purity
- Reduce loss of valuable chemicals
- Minimize undesirable atmospheric emissions to reduce air pollution
Why Choose Demister Filter From Filson
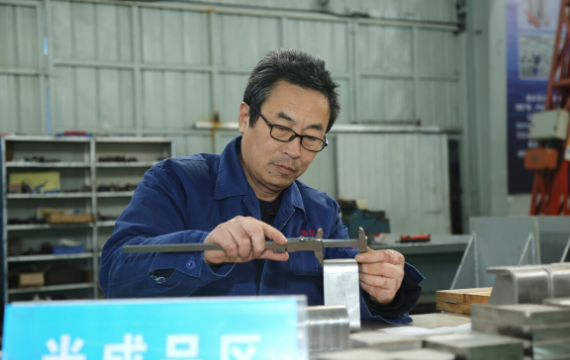
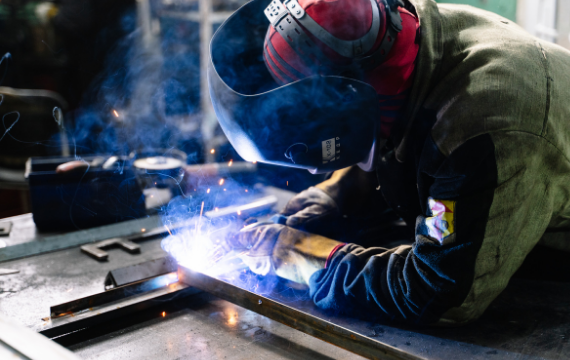
Filson is a professional manufacturer of extremely high quality demister filter in China. We offer various types such as mesh demister pads, vane type demister filter, fiber bed demister filter, cyclone demister filter.
Filson demister mist elimination systems are available for almost all liquids and gases that need to be separated. Whether your need is for demister filter, coalescers or vane units, Filson has you covered. When you need them now, require a quote, and we will provide you with the service and quality you expect and deserve.
Filson also can offers the replacement of other brands demister filter, such as york mesh demister, Otto York demister, Koch Glitsch demister, AMACS demister, York 421 demister, Munters demister, Sulzer demister, etc.
At Filson, we have a full range of mist eliminators (demister) to ensure a customized solution for your application. If you have any questions about demister filter, please feel free to contact Filson. Our experts are available 24/7 to help you solve your problem.
- Raw material: Nickel, Titanium, SS304/316L, Brass, Copper, Inconel, Monel, PP, PTFE, PE,PVC
- Mesh Wire Diameter: 0.15-0.35 mm
- Pad Diameter: 300-6000 mm
- Pad Thickness: 100-150 mm
- Pad Type: mesh, vane
- Separation Efficiency: 94-99.9%
- Filtration Accuracy: 0.1-50 micron
Note: specific design is customized, please contact Filson freely.
- Oil and gas production
- Power generation
- Chemical industry
- Petroleum refineries
- Medicine industry
- Sulfate industry
- Light industry
- Metallurgy industry
- Pulp mills&Sugar mills
- Environmental protection
Demister Filter: The Ultimate FAQ Guide
Here is a complete guide with answers to any question about demister filter.
It will help you explore the design, best material, maintenance procedures, working principle and components of demister filter, amongst others.
By the end of this guide, you will definitely be an expert in the demister filter industry.
Have a look:
Demister filter is a device regularly fixed to liquid-vapour separation vessels thereby removing droplets of liquids and coarsest particles from the vapor stream.
Demister filter
The best position for installing the demister is above the liquid surface or upstream.
Such that the incoming vapor passes through the demister filter at a specific velocity.
The demister filters, therefore, serve as a pre-separator medium in cases whereby you suspect the vapor to be contaminated or if it is indeed infected.
Generally, demister filters, therefore, filters gasses or liquefied gas.
They are available in a wide range of varieties.
Similarly, demister filters are also known as aerosol filters, mist filters, or deep bed filters.
Besides liquid droplets, you could as well separate solid particles/ dust (coarsest particles), and aerosols from the liquefied gas.
You can only achieve this to some extent using the demister filters.
However, that does not necessarily mean you cannot altogether remove those two sets of particles (dust and aerosols) using the filters.
Indeed, some demister filters are efficient in removing those extracts.
So, that makes the removable components to be majorly three, i.e., dust, liquid droplets, and aerosols.
You need to use demisters where achieving vapor quality is your top priority regarding suspended liquids or solids.
Furthermore, the Demister filter is a suitable pre-separator where foreign particles highly contaminate the vapor.
At a basic functionality level, demister filters would remove contaminants of very exact sizes of 1µm, 2µm and more.
Dust particles being especially bigger compared to droplets.
Besides guaranteeing fluent filtration of vapor, the demister filter also prevents any possible loss of products and protecting the equipment from damage.
Demister filter
As earlier pointed, demisters are incredibly efficient and would optimally yield a removal rate of a maximum of 99% for the aerosols, dust, and liquid contaminants.
This level of efficiency is only achievable at a minimum pressure drop.
Nevertheless, the efficiency again would vary depending on two vital factors—the first one; the mesh sizes of the filter elements.
For example, demisters with filter elements which have got mesh sizes ranging 1µm to 3µm are more efficient compared to those who have a more significant mesh dimension.
The only problem is that those filter elements are at considerable risk for blockage.
Secondly, the efficiency of the demister filters much depends on the sizes of the contaminants.
Removal efficiency is highest (99%) for particles with bigger sizes say 10 microns and more.
Whereas, efficiency declines for particulate of tiny sizes ranging between 1 micron to 5 microns and submicron particles.
Nevertheless, the efficiency can still clock 99% when the demister filter has a large free volume of a maximum of 99% and a big surface area.
Above all, different manufacturers apply varied mechanisms and technology in producing demister filters.
Therefore, there would be a possible difference in its efficiency.
That is why you have to partner with a reliable manufacturer who produces pure quality.
Conventionally, demister filtration systems are applied in applications where there is a great need to separate liquid droplets from flowing vapour consistently.
Such functions are several and diverse.
For example, in marine applications, specifically naval vessels, demister filters reliably separate liquefied droplets of salt from brine vapor during the desalination of brine.
The process involves: flash heating brine to form a vapor.
During flash heating, the resultant gas would contain brine droplets, which should be eliminated before reaching the level of condensation.
If not, the distillate vapor would likely contain salt.
The demister filter then filters the vapor, which upon filtration of brine droplets (salt) would condense later on in the desalination plant tubes.
The distillate tray then collects the condensed product liquid.
Additional notable applications of demister filters are in:
- Cushioning the compressor compartment from the entry of fluid or degassers in compressor suction lines
- Steam drum evaporation demisting system.
- The gas scrubbing demisting structure to recover introduced droplets.
- Exhaust demisting system for recovering dangerous liquids.
Other applications:
- Absorption pillars
- Steam boilers
- Gas-air scrubbers
- Desalination plants
- Distillation columns
- Oil/ mist separators
- Flame arrestors
- Gas treatment
- Phase separator equipment
- Separator vessel
- Gas-liquid separators
- Vapor-liquid separator
- Ammonia and chemical fiber production
- Desulfurization
- Extraction of oil mist
Demister filters have woven like filter elements of a metallic structure or synthetic.
The necessary process involves directing a stream of gas through a specific configuration of filter elements.
Separation then occurs at the filter material.
But now, separation of droplets takes place via three essential mechanisms, i.e., Inertial impact, direct impact, and Brownian motion capture.
Inertial impact: The droplets present in the vapor possess momentum, which directly varies with the density of the liquid and the cubic diameter.
Thus the more robust or more significant particles would appear to resist flowing in the streamline of the pumped gas, in turn striking any barrier in their direction of travel.
And that is the inertial impaction.
This mechanism is capable and responsible for extracting primary particles of sizes larger than 10µm.
Direct impact: besides bigger particles, the smaller particles present in the streamline flow potentially collide with the solid objects/ barriers.
That occurs in case their displacement is lower than their structural radius.
Often, particle sizes ranging between 1 to 10 µm get eliminated in this manner.
Brownian motion capture technique: it wholly relies on the Brownian motion (i.e., the non-stop random movement of droplets under elastic collision with gas molecules).
As the particles get tiny, the velocity drops, and the Brownian capture increasingly becomes efficient in removing them.
Therefore, it is the dominant extraction mechanism for submicron droplets.
Note; the indicated barriers in the case above refers to the filter elements(wire surface)
The resultant trapped droplets would then collect at the crossover sections in the mesh.
The accumulating liquid droplets afterwards form more massive, heavier drops that move downwards, at which they gather at the bottom.
Important: the working of the demister filter is also directly proportional to its design.
On the other hand, the design of the demister filter also depends significantly on operational conditions.
They include volumetric flow rate, particulate type, the medium of separation, and the separation operation.
Vane plate demister filter
i. Resistant to adverse conditions such as acid and alkali, no wonder they are favorable for use in chemical and oil industries.
ii. They are manufactured in Varied shapes and sizes for fitting in the horizontal or vertical flow direction.
Furthermore, any manufacturer can comfortably customize the shapes, sizes, and supporting grids to suit customers’ wants.
iii. It should be acid, heat, and rust resistance.
iv. Convenient to install and maintain: demister filters are easily installed in any grid.
Even if they got big diameters, you could disintegrate the demister pads into several parts for easier installation and transportation.
Moreover, they have very few components and do not break down, therefore easier to maintain.
v. Several and customizable choices of materials: you can choose between metallic or non-metallic materials demister filters.
This will be according to the withstanding usage conditions and filtering necessaries.
vi. They have a simple structure and light in weight.
vii. Have a large surface area and low-pressure drop.
viii. They have a longer service life.
i. Highly efficient when removing entrained liquid droplets from the pumped gas.
Well, a designed demister filter completely removes approximately 100% of the contaminants.
ii. Suitable for filtering aerosols, droplets, and dust.
iii. Capable of self-cleaning when capturing liquid droplets.
iv. Easy to operate.
v. It does not cost much for initial capital and has available spare parts.
Though not significant, the demister similar to other devices have the following disadvantages:
I. Highly susceptible to blockage, especially for the small-sized mesh filters.
II. The high pressure decreases when the filter captures solid particles.
III. The aftermath of cleaning the filter is dirty, scrubbing liquid.
Demister filter
Your options are never limited when it comes to choosing a demister filter that is favorable for your work conditions.
You can find the demister filters with the following material structure, namely: Stainless steel (316 SS, 304 SS), Alloys such as 20, 200, 400, 600, 800.
Other materials include Aluminium, Copper, Halar, Kynar, PTFE, PVC, Polypropylene, Titanium, Tantalum, Galvanized wire, nylon yarn, glass fiber, polyethylene, Nickel wire.
The primary objective of filtering vapor is absolutely to produce high-quality gas at the expense of the entrained droplets and dust.
Besides, it also protects the environment from harmful pollutants that would have been released, for example, in chemical and oil industries.
Lastly, filtering gas is essential in improving process safety.
The demisters can generally fall into four categories, i.e., mesh, vanes, cyclones, and fiber beds.
1. Mesh
A knitted mesh comprises various materials and even densities depending on the manufacturer’s specifications.
Some meshes, though, consists of varied interwoven elements to capture different types of fluids such as condensate and glycol.
When vapor passes through the mesh, pure gas freely passes while the liquid droplets via inertia fall onto the wire surfaces.
They accumulate and eventually drain out into droplets.
2. Vane
Vane types are available in a variety of designs but majorly single and double pocket design.
When you pump liquefied vapor through the vane, the gas stream passes via parallel plates, which makes it change directions several.
Centrifugal forces then make the liquid droplets separate from the vapor on the vane blades.
The collected liquid then falls from the blade slits.
Importantly, the vane efficiency depends on the number of vanes, inclination of the vanes, sizes of the liquid droplets, and the distance of separation amongst the vanes.
Vane type demisters are widely applicable in oil/gas separation and suitable for extracting droplets of 8µm to 10 µm.
To enhance the vane efficiency, you may install an agglomerator upstream.
3. Cyclones
Cyclones are increasingly gaining popularity due to their capabilities of being highly efficient at high pressures.
Besides, they have four times the capacities for gas and liquids compared to either mesh pads or vane packs, respectively.
Finally, cyclones are suitable for foam breaking and non-fouling.
Cyclones are additionally easy to install horizontally or vertically.
Plus, the cyclones do not suffer from deposition due to their high velocities operation.
The demisting cyclones are, in turn, classified into three categories, i.e., Reverse flow, non-recycling axial flow, and recycling axial flow.
4. Fiber Beds
Fiber beds are typically cylindrical when packed.
Their operation involves the flow of vapor through numerous filter media layers.
Every layer, however, consists of progressively bigger average pores opening.
Now, when the droplets struggle to pass through open pores, they will blend.
This process continuously proceeds cyclically until the more significant drops collect and drains into the collecting sump.
The average removal size of particles for the filter bed type is about 0.3 µm.
For the capture of small liquid droplets, the fiber bed demisters have tiny diameter fibers of about 0.02 mm and employ the Brownian diffusion technique.
Besides, they remove drops of up to 0.1 µm.
Demister filtration system
Demister housing is the overall mechanical out structure of the demister filters.
The housing majorly filters and collects tiny droplets from the purified gas stream.
Besides, the filter housing should be structurally strong to contain flow rates of approximately 125 cfm up to a maximum of 10,000 cfm and more.
Moreover, the demister housing comprises of three distinct pieces.
- Lower housing- occupies the down end of the filter.
- Demister element clamping frame – used for attaching both the lower and upper housing sections.
- Upper housing – occupies the top part of the filter.
Also, for you to attach both the upper and lower housings, you will require bolt flanges.
With that, you obtain flanged housing ends that conform to regular ANSI size for field-bolting into the vapor stream.
The component housings should be of a suitable material resistant to corrosion, rust, and harsh chemicals.
Such kind of material is the Type -304 stainless steel made of level 4 (#4) finishing on the entire exterior surfaces.
Depending on your usage and mode of application, you can easily incline the demister housing horizontally or vertically.
Most importantly, you need not worry about the overstretched sizes of demister housing.
Remember, the manufacturers easily customize the dimensional specifications of the demister housings and elements into suitable sizes.
Modifications of the dimensional structure are vital to enable it to fit into the constraints of any vapor flow system.
Concerning the Succinct features and specifications, we can widely classify demister filters in terms of their efficiency in the following distinct classifications:
6Gas demister filter
- Standard type
- High-efficiency Type
- High Permeability Type
- Shock Absorption Type
Standard model: this is a typical ordinary demister filter that functions optimally, nothing outstanding in its features.
However, it would sufficiently guarantee you well filtration of your gas stream.
Material: stainless steel 302, 304, 304 L, 316, 316 L, 317, galvanized iron wire, copper wire, polyamide fiber, PVC fiber.
Common Diameter: falls in the common range ie. 0.1 mm, 0.2 mm – 0.4 mm, 0.45 mm
Weight capacity: approximately 168 Kg/ m ³
Surface area: about 529.6 m²/ m ³
Porosity: 0.9788 ɛ
High Efficient Demister pad Type
Material: Stainless steel 302, 304, 304 L, 316, 316L, 317, Polyamide fiber
Common Diameter: ranges between 0.12 mm to 0.45 mm.
Weight: 128 kg/m³
Surface area: 403.5 m²/m³
Porosity : 0.9839 ɛ
High Permeability Demister pad filter type
Wire materials: stainless steel wire
Wire diameter: 0.1 mm × 0.4 mm
Shock Absorption Demister Pad type
Material: stainless steel 302, 304, 304 L, 316, 316 L, 317,
Common diameter: 0.21 mm
Weight capacity: 168 kg/ m³
Surface area: 529.6 m²/m³
Porosity: 0,9788 ɛ
Please note that the above technical parameters and dimensions are a reference point.
Therefore, you are free to contact a manufacturer to customize your specifications.
Selecting a suitable demister filter is a significant step to ensuring that you obtain a quality vapor, free from micron-sized liquid droplets.
Here is how you need to go about it:
· Consider the Material Type
The range of material choice and selection is very diverse for the demister pad.
In fact, the list ranges from metallic materials to non-metallic ones.
Also, the metallic include galvanized steel, stainless steel, copper steel, monel.
Moreover, the non-metallic material structure includes PP, PVC, PE, and PVDF materials.
Also, the material should be one that is resistant to adverse functionality and usage conditions such as corrosion, rust, temperature, high pressure, and chemical resistance.
· Choose a suitable Demister Pad Shape and Dimension
The available demister pad shapes include rectangular, ring-shaped, unique shaped, and round shaped.
However, there are several other customized shapes according to the customer’s specifications.
The pad dimension should also be one that fits into the opening of your tunnel.
Besides, the shapes and sizes are customizable.
· Selection of Supporting Grid
It is essential to reinforce and increase the rigidity of the demister pads, to do that, a variety of strips come in.
Besides, assembling the strips/ grids onto the filtering devices is simple.
The grids include round bar supporting strip, flat strip supporting grid, round bar and flat piece supporting grid, crimped wire mesh, and supporting grid.
· The Appearance of the Demister Pads
Most Manufacturers construct the demister pads into smooth and separated parts. It could also be into waveform structures.
The basic appearance models are standard soft kind and particular wavelike forms.
· Take into Consideration the Structural Type
The small diameter pad is always structured into full integral pads.
However, the large diameter pads are commonly structured into disintegrated parts to enable easier installation and transportation.
Thus, your primary options are distinct pads and separated part pads.
Yes, it is advisable to often clean the demister pads.
Subsequent and continuous filtration of vapor would lead to continual accumulation of liquid droplets, dust, and aerosols on the demister pads.
Such collection is dangerous because it would finally cause plugging and blockage.
This in turn severely affect the performance of the demister pad.
The conventional technique of cleaning the filter is via rinsing.
Every use of the demister filter will lead to continuous trapping of droplets at the pads.
Even though a demister filter has a long service life, you will need to replace the demister filter occasionally.
But you only need to do the replacement once you deem the demister pad unsuitable for conducting continuous filtration of vapor.
The dilute acid present in the demister pad is also another condition that may likely shorten its durability due to corrosion.
Depending on your usage, manufacturers recommend that you replace the demister pads every 30 days or a couple of weeks for cheaper material structures.
Above all, specialists recommend replacing the demister pad once it reaches a 20% declination in its wire mass, and that would significantly increase the efficiency.
Stainless steel demister filter
i. The extent of usage – the lifespan would depend on your industrial needs.
If you occasionally use the demister filter and up running for a few hours a single day, then a single demister pad can last for about a month.
Also, iF your demister filter is continuously operating, then you would need to change the filter pads every few weeks.
That is especially ideal if you are using a cheaper option of fiberglass pads.
ii. The vapor quality- the type of liquefied gas would also affect your demister pads replacement cycles.
The highly contaminated or toxic gas, for example, industrial emissions that contain acidic components may quickly destroy the pads.
iii. The type of material structure – some materials are susceptible to corrosion and rusting compared to others.
For example, fiberglass is easily degradable in comparison to stainless steel.
Note that the correct installation of the demister is the surest way to maximize its performance.
Again, demister pads come when already slightly oversized to take care of any possible deformation of the vessel.
Secondly, to ensure a tight fit on the vessel wall to avoid possible gas leakage on the wall surface.
First Step: Inspect the New Demister Pad
Check if it is the right type you ordered.
Confirm its dimensions if it is consistent with that of the drawing—Check-in case of any mechanical damage.
Finally, store the pad in a dry and tidy place.
Second Step: Take out the Old Demister Pad
Take note of how the old demister pad was installed.
Check if it has got existing corrosion or fouling or dislodged parts.
After that, remove the demister pad piece by piece.
Check for any cracks, damaged support grids, and excessive corrosions on the support structures and repair all the possible defects.
The deformities would potentially hinder the installation of the new pad if not well serviced.
Third Step: Installation of the New Demister Pad
Installation procedures of the demister pads vary depending on the following factors.
- The type of the demister pad, i.e., single-piece demister pad and multi-section demister pad
- Mode of inclination of the vessel- is the vessel vertical or horizontal?
- The Inclination of the demister pad, i.e., horizontal or vertical demister pad.
- Nature of the support rings/ grids in the vessel: some vessels have one support ring while others have dual support rings.
However, no matter the appropriate installation format for your application.
You will also select a proper mode of hold-down technique/ fastening method from the available options: tie wires, J-Bolts, Latch Keys, dual support rings, offset rings, hold-down bars, Basket cages, expansion rings.
Fourth Step: Finishing
Once you complete all the installation procedures, you need to verify the following:
Check for the presence of any gaps amid sections and rectify where possible.
The demister pad should be fitting compression fit uniformly.
Ensure your tied-downs are secure, the rings and beams sufficiently support the demister pad.
For dual design demister pads, ensure that you install all the sections corresponding to the right flow orientation.
Finally, remove all the working tools and materials from the demister pads before switching on.
The essential routine maintenance of the demister filter is cleaning and replacement.
· Cleaning of Demister Filter
The trapped solids in the demister pad over time will cause plugging, which leads to abrupt pressure drop and performance.
Therefore, the basic routine would be proper cleaning.
And you need to do the cleaning before the accumulations are severe and before the performance of the demister plug considerably deteriorates.
So you will require a spray system that regularly or intermittently sprinkles wet the demister pad to reduce plugging.
However, you could also choose to either spray the demister pad with a cleaning liquid, soak the pad, or pass steam through the pad.
But be sure that whichever cleaning technique you apply, it will not destroy the mesh pad.
Some specialists also advise complete removal of the demister pad for effective or thorough cleaning.
· Replacement of Demister Filter
At some point, you may consider replacing the demister pad depending on the extent of plugging and corrosion.
You should follow this simple process:
i. Pressure Drop
You need to monitor the pressure drop across the demister filter constantly.
As a rule of thumb, record the initial pressure drop during start-up after clean- up for future considerations.
i. Issue – Increase in pressure drop beyond an inch of the water column above start-up requirements.
Reason – potential plugging.
Solution – clean the mesh pad.
ii. Issue – decrease in the pressure drop
Reason – holes in the pads, decreased mesh density.
Solution – replace the demister pad.
With this information, you should be able to choose a suitable demister filter for your application.
But, even as I conclude this guide, you could be having more questions.
Or, you need assistance on demister filtration systems. You can contact us now for free consultations.
Generate the CSS style for border radius, fonts, transforms, backgrounds, box and text shadows with the online CSS code generators.