Your Reliable Heat Exchanger Supplier in China
Filson heat exchanger is a system used to transfer heat between two or more fluids. Commonly, heat exchanger is applied to both cooling and heating processes to realize its excellent heat transfer property.
Filson carries a complete series of heat exchangers including but not limited to plate heat exchanger, plate and shell heat exchanger, shell and tube heat exchanger, stainless steel heat exchanger and tube fin heat exchanger.
Filson is a quality-driven company which manufactures high grade heat exchangers and satisfies customers specifications by using the advanced equipments and latest technologies. So Filson swears to bring the best and perfect products to you.
View the following article about Filson heat exchanger to know what a heat exchanger is or how heat exchanger works. It will also help if you don’t know which type of heat exchanger is most suitable for your applications.
Filson Heat Exchanger
Why Choose Filson Heat Exchanger
Filson has rich experience in designing, manufacturing and even customizing frequently-used heat exchangers. No matter how special your requirements are, Filson will try best to build a perfect one for you.
All your heat exchangers are promised to be delivered within 20 working days and if there are products in stock, you can receive them earlier. Also, a free sample is allowed to be provided before your larger order within 7 days, so that you could check all details of Filson heat exchangers.
- Over 20 years heat exchanger manufacturing experience
- Take care of every detail of manufacturing process
- The most reliable and professional heat exchanger manufacturer and supplier in China
- Advanced testing equipment and strict standards to ensure and control heat exchangers quality
- Top quality raw materials that are fully certified
- Long warranty period over one year for all our heat exchangers
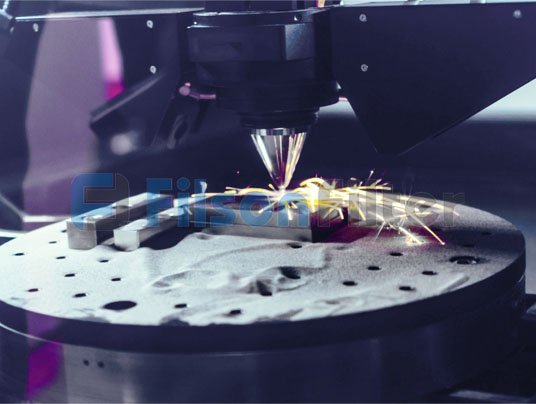
Filson: The Optimal Heat Exchanger Choice for the Application
Through 20 years designing and manufacturing experience in the field, Filson has acquired valuable knowledge and expertise of heat exchangers. We guarantee high performance and the long lasting of our products by implementing a strict quality management plan.
Filson now is committed to constantly upgrading and developing heat exchangers by incorporating feedback from our customers all over the world and in-house testing facilities. All these are produced under the support of our advanced software for thermal and mechanical calculations.
Generally, in a Filson heat exchanger, there are two kinds of fluids with different initial temperatures flowing through for heat exchanging. The fluids may be separated by a solid wall to prevent them from mixing or sometimes they may be in direct contact.
Filson heat exchanger is mostly made of metals for their quick absorption and siginificant conduction of heat, such as stainless steel, carbon steel, duplex stainless steel, aluminum alloys, etc. But sometimes, they can be made of ceramics, composites and even plastics.
Filson heat exchangers are manufactured using fully certificated raw materials. All these materials have their advantages. Ceramics and metals can be best choice when comes to high temperature and corrosion circumstances, while plastics have relatively lighter weight and lower cost.
With different manufacturing materials and types metioned above, Filson heat exchangers have the ability to perform in various industrial applications including waste water treatment, refrigeration, wine and beer making, petroleum refining, nuclear power and chemicals.
The adoption of a Filson heat exchanger will greatly improve your industrial energy efficiency by transferring heat from systems where it is not needed to other systems where it can be fully used. Then your company will run better and profit more.
The efficiency of a heat exchanger means how well it performs in transferring heat relative to the pressure loss it produces. Typically, Filson heat exchanger allows a rapid flow within it to facilitate the heat transfer.
The rapid flow may result in pressure losses in the fluids. Compare to common heat exchangers, Filson shows its advantages on this occasion. Our proven and mature heat exchanger technology minimizes pressure losses while maximizing heat transfer efficiency.
Filson heat exchangers can meet multiple design goals like resisting high fluid pressures, withstanding fouling and corrosion. Of course, regular cleaning and repairing is required after a period of use. And our specialists will provide you the right cleaning methods.
The size and shape of Filson heat exchangers is available to be customized. If you have the needs for a well-performance heat exchanger, Filson will always be your best choice and we are here ready to help anytime.
As one of the most professional industrial heat exchanger manufacturers in China, Filson possesses the best resources for your custom heat exchanger. Looking forward to being your heat exchanger partner in the future!
How Does A Heat Exchanger Work?
Different Flow Types in Heat Exchanger
The picture showed above is a basic and simple working principle of a Filson heat exchanger.
Regardless of the types, designs and materials, all heat exchangers operate under the same fundamental principles.
Filson heat exchanger is a device that allows heat from a fluid to pass to the other fluid without the two fluids mixing together or contacting directly. The fluids can be either liquid or gas.
Take the picture for an example:
The hotter fluid flows through the red area, at the same time, the cooler fluid flows through the blue area. During this process, the hotter fluid transfers its heat to cooler fluid and becomes lower in temperature, while the cooler fluid absorbs heat from hotter fluid and becomes higher in temperature.
Filson Heat Exchanger Function:
- Optimize the overall energy system
- Improve energy efficiency of plant systems
- Reduce fuel usage, greanhouse gas and emissions
- Heat a cooler fluid using the heat from a hotter fluid
- Cool a hotter fluid by transferring its heat to a cooler fluid
- Boost profits by saving energy
- Benefit a wide range of industries
- Improve sustainability and lower environmental impact from waste energy
Filson Heat Exchanger Feature:
- High energy efficiency
- Optimal heat transfer with minimal operating costs
- Extremely durable and permanently sealed
- No or small amounts of cleaning and maintenance necessary
- Easy and fast installation, cleaning and replacing
- Excellent endurance in heavy industrial conditions
- Sophisticated design for minimal footprint
Filson Heat Exchanger Specification:
- Material: stainless steel, carbon steel, cemaric, plastic, graphite and more
- Media type: oil, water, air, gas
- Working temperature: under 450℃(up on material and type)
- Working pressure: under 6.4MPa
- Flow rate: 25L/min(depending on fluid type)
- Heat transfer efficiency: 2.80% to almost 100%
- Heat exchange area: 1 – 800㎡
- Color: grey, blue, silver, brown(based on customer requirements)
- Standard: ASME, ANSI, JIS, GB
Filson Heat Exchanger Application:
- Dairy, food or beverage industry
- Engine cooling
- Hydraulic oil cooling
- Evaporator and condenser applications
- Refrigeration industry
- Solar heating
- Water cooling and heating
- Power plants
- Chemical processing
Heat Exchanger: The Ultimate FAQ Guide
heat exchanger is an equipment that helps in the transfer of energy between two or more fluids.
Or, it can transfer heat between a solid object and a fluid.
Heat exchanger system
In essence, one fluid provides heat while the other receives heat.
These fluids are separated by a solid wall to aid in preventing mixing as they could come into contact.
An example of a heat exchanger is a heat sink that passes on energy produced by a mechanical or electronic device to a liquid or gas coolant.
A heat sink is a passive heat exchanger.
Another example is that of a device in an internal combustion engine where an engine coolant passes via radiator coils and air goes past the coils.
Thereby cooling the coolant and heating the incoming air.
One of the demands for design process specifications is that fluids at kept at a specific temperature.
Also, the minimum requirement for this device is the availability of two media streams having different temperatures.
One of the media streams has a heat supply while the other has a heat receiver.
You can use heat exchangers in either the main or auxiliary process.
The construction and design of this device is governed by the TEMA and ASME codes.
A heat exchanger is known for two main components – a number of tubes inside a cylindrical shaped shell.
Parts of heat exchanger system
However, there are several components which range from:
· Tubesheet
Normally, two tube sheets are needed for this device.
A tube sheet is a plate drilled to avail of holes via which tubes can be inserted.
Attached securely to the tube sheet are tubes that help prevent the fluids from mixing with one another.
The holes that are drilled in the tube sheet take either a square or a triangular pattern.
Once you have inserted tubes via the holes on the tube sheet hold it firmly via hydraulic/mechanical expansion or by welding.
Heat exchanger tube sheet
· Tube Bundle
A tube bundle consists of several types of tubes ranging from longitudinally finned, to plain tubes.
They are the parts of the device through which fluids run through.
Heat exchanger tube bundle
· Tubes
These are pipes with small diameters often located inside a shell and securely attached to tube sheets.
Tubes can be arranged in triangular or square patterns.
Square patterns guarantee clear lanes for cleaning the tube’s outside surfaces.
On the other hand, triangular patterns guarantee better heat transfer on the tube’s outside surface together with more turbulence.
Heat exchanger Tube
Baffles
Baffles are often used in heat exchanger shells to direct to guide the fluid stream over the tubes.
Hence, increasing the heat transfer coefficient and the velocity of fluid flow.
Baffles help reduce vibration in the tubes as well as indirectly support the tubes.
Also, it helps maintain the tube spacing.
Heat exchanger baffle
Heat exchangers have baffled tubes that direct fluid to facilitate four passes via the tubes for more efficient heat transfer.
Baffle pitch is spacing between the segmented baffles.
Baffle cut, on the other hand, is a segment cut to allow the fluid to flow parallel to the tube axis as it moves from one baffle space to the other.
Both the baffle pitch and cut are often chosen during the design process of the device.
This activity helps provide high heat transfer and fluid velocity rate while heeding to the allowable pressure drop.
· Shell
This is the most expensive part of a heat exchanger.
The diameter of the shell will depend on the diameter of the tube bundle.
According to the TEMA rules, a shell size ranges between 6 inches to 60 inches.
Further, they have standard pipes that can go up to 24 inches.
You can fabricate a shell size more than 24 inches through rolling a plate.
Heat exchanger shell
· Plates
Plates are often separated by gaskets.
There are several plates securely attached to the shell of the device.
You can change the contact surface area of heat exchangers by removing or adding plates.
The service of the plates can be easily limited by pressure ratings.
Plate heat exchanger
· Spiral Tubes
A spiral tube is a small pipe with a small diameter but comes in a spiral shape.
This tube is welded well to the shell to ensure strength and durability.
Spiral tube heat exchanger
· Spacers
Spacers help maintain the space between baffles.
They are often passed over the tie rods.
Because of spacers, baffles cannot slide over tie rods under the effect of the liquid’s force.
They also hold the baffle assembly in one place.
The minimum number of spacers depends on the diameter of the device as well as on the size of the spacers.
Spacers in heat exchanger system
· Gasket
Gaskets are manufactured in different shapes, sizes, with or without bars.
While the other gasket is the secondary seal, the inner diameter of this feature is the primary seal.
The type of gasket chosen for a heat exchanger depends on the operating conditions of the device.
Some potential gasket materials are rubber and fiber.
Gasket in heat exchanger
· Tie Rods
Tie rods just like spacers are an important component of heat exchangers.
Tie rods are secured to one end of the last baffle and to one end of the tube sheet.
The many tie rods you have in your device depending on the size of the tie rods and the diameter of the shell.
Tie rods in head exchanger system
You have to perform all the necessary inspections and tests you deem necessary for your applications.
In fact, the test should be according to the set production and operation codes.
As a customer, you can always check product certifications to ensure quality of heat exchangers.
Otherwise, the below certifications and tests have to be performed on heat exchangers to ascertain their quality.
Quality Tests
Some of the quality tests include:
I. Hydraulic Test
The hydraulic test is done mainly on the pressure containing parts of a heat exchanger.
The main parts are bundles of a tube, end cover, and shell of a heat exchanger.
The testing pressure is 1.5 times that of the design pressure and it lasts around 15 minutes.
II. Eddy Current Testing
This test is mostly used on non-ferromagnetic tubular.
It characterizes, detects, and sizes tubular flaws.
And, this includes cracking, wall thinning, subsurface voids, and de-alloying.
Usually, tubes are subjected to heavy stress as a result of high fluid pressure, contractions and expansions of the tubes.
It is the most ideal inspection method as it detects key stress points in the tubes of heat exchangers.
III. Penetrant Examination Test
This test is done to determine uncommon and common discontinuities open to the surface of the material.
You are highly likely to come across findings such as grinding cracks, fatigue cracks, weld discontinuities, impact and overload fractures.
IV. Internal Rotary Inspection Systems
IRS is done to test the interior and outside diameter non-ferromagnetic and ferromagnetic heat exchanger tubes for corrosion.
The process involves the use of mirrors that produce an ultrasonic pulse close to a helical path to yield a scan and appropriately measure metal loss and wall thickness.
V. Remote Field Testing
This test is to examine tubes for thinning.
It is applied on ferromagnetic tubing.
You will know of flaws if the magnetic field shows distortions.
VI. Radiography Test
A radiographic test is to determine the quality of the weld joints between the special connection fittings and the device’s spiral manifolds.
This test involves taking an X-ray of the welds to confirm that there is no cracks or porosity.
A sensitive leak test is done after the radiography inspection.
It involves applying pressure to the assembly coil using helium.
Further, you use an ultrasensitive helium detector to make sure that there are no leaks in the coil assembly.
This analyzer easily detects a helium leak that equals 1×10-9 cc/second.
The moment the specific heat exchanger passes the coil assembly test a client is guaranteed of the quality and performance of the device.
It, therefore, saves one time and money.
VII. Helium/Air Tightness Test
This test is done to determine the leak tightness.
It is done using helium leak detectors and helium.
The process involves measuring the helium concentration in the tube’s volume.
The value of the leak rate has to be calculated.
VIII. Hydrostatic Test
This test is done on a device’s complete bundles and other parts.
The amount of test pressure has to be consistent with the value shown in the approved drawing.
This test is successful only if there is no leakage or pressure drop while the device is under pressure.
After conducting all quality tests, you have to do thorough inspections of all parts of a heat exchanger.
This is to determine if they have any manufacturing defects.
This type of test/inspection is referred to as a whole unit test.
IX. Expansion Joint Inspection
Those heat exchangers with expansion joints undergo this type of inspection.
However, the inspections are for:
- Air test
- Inspecting the internal surface most especially for erosion and corrosion
- Inspecting the flanges for corrosion and erosion
- After all these inspections and tests, you conduct the hydrostatic test on the device.
Certifications for Heat Exchanger Systems
Some of the main certifications are:
· ASME Certification
This certification tells clients that the chemical composition, strength, and pressure ratings and testing of a device’s materials adhere to the industry’s strictest quality mandates.
The manufacturing plant in which heat exchangers are manufactured must comply with the ASME Code.
The products from the plant must receive a Pressure Vessel designation which comes in the form of a (U-stamp).
It guarantees the device’s alignment with written ASME specifications, procedures, and test requirements.
· Non-destructive Certification
Level III NDE inspection is done to approve radiographs before continuing with product finalization.
· ISO9001 Certificate
Heat exchanger must have an ISO9001 quality certification.
This quality mark assures the buyers of the high quality and safety of the heat exchanger.
· CE Certification
This is a quality assurance certificate.
CE mark shows adherence to safety, health, and environmental protection standards for heat exchangers sold within the European Economic Area.
Tube heat exchanger system
Heat exchangers can withstand very high temperatures and pressures.
It all depends on the buyer’s specifications.
For instance, a shell and tube heat exchanger can withstand a pressure of 30 bars and a temperature of 2600C.
Similarly, a plate heat exchanger can operate at temperatures as high as 5000C.
Plate heat exchanger
This information shows that the temperatures and pressures of this device vary depending on the types of heat exchangers.
Depending on the technologies used, the pressures and temperature that this device can withstand range up to 1000 bars and 1000°C.
Below are some of the advantages of a Heat Exchanger:
- There is a larger heat transfer area
- Can withstand high pressures and temperatures.
It can, therefore, be used in systems requiring higher operating pressures and temperatures.
- Are highly durable as they are made using material with high tensile strength
- They are protected from corrosion
- There is high heat transfer efficiency
- It is lighter in weight seeing as it is made using a material with this unique property
- Are highly expandable, especially plate and frame heat exchangers.
You can increase its capacity by bringing plates in pairs.
- Have low downtime
- Since the pressure test is easy, you can easily locate and plug tube leaks.
- Some are suitable for viscous products such as shell and tube heat exchangers.
Due to the high turbulent flow, this device does not leave behind deposits which could interfere with heat transfer.
- A small foot print such as plate and frame heat exchangers.
Besides, they are good for the environment as the device consumes low energy while maximizing the process effect and reducing cleanliness.
- Have maximum reliability; with this, there is reduced stress, wear, scaling or corrosion.
- Heat exchangers, therefore, function at their optimum level.
Ø Versatile
This equipment has many applications in the industry.
For instance, you can a heat exchanger in a chemical plant, sewage treatment, petroleum refineries, and nuclear power facilities.
Internal combustion engines have a radiator coil which is an example of a heat exchanger.
Ø Maintenance
This device is often easy to clean due to its CIP design.
The present devices have been modified, especially with ease of cleaning in mind.
For instance, you can easily remove the plates of a plate heat exchanger and replace them individually.
With this device, you do not have to remove the whole system when cleaning.
Ø Cost
As technology progresses so does the fabrication cost of heat exchangers.
Most of the modern heat exchangers use pressed plates, which are not as expensive as welded plates used in the old models of this device.
Besides, pressed plates exhibit excellent properties such as more resistance to chemical reactions and corrosion.
These reactions often weaken this device requiring more repairs and replacements.
This equipment is, therefore, sold at competitive prices even though some may find them a bit costly.
Ø Adaptable
The majority of the modern heat exchangers, especially plate heat exchangers are highly adaptable.
The adaptability features make this device suited for a wide variety of applications.
This device can be used in smaller items as the current ones have become more compact.
Today heat exchangers are even used in air room conditioners and portable showers.
Heat exchangers are flexible as the fluid used to facilitate the thermal transfer process can be modified to design specifications.
There are different factors involved when choosing the best heat exchanger.
Some of the factors you should consider when choosing heat exchanger systems include:
· Structural Strength
The heat exchanger has to be durable and strong.
Its shell must be able to withstand high pressures and temperatures.
· Size
More heat transfer is highly likely to occur if the contact surface area is great.
When selecting a heat exchanger, choose one that fits your specifications/needs/requirements.
· Cost
Typically, a heat exchanger has a high initial cost and lower maintenance and repair costs.
If you pay a high initial cost for this device, you will spend less on its installation and maintenance.
However, if you pay less initial cost, you are highly likely to spend more money on the installation and repair costs.
The device will not last long forcing you to buy another heat exchanger.
As such, the cost of a heat exchanger is very important when selecting a suitable device.
· Pressures
You have to consider the amount of pressure that will be applied to the heat exchanger.
Some of the pressures involved are acceptable loss of head, design pressure, maximum service pressure, etc.
Shell and Tube Heat Exchangers are the most preferable devices because they can withstand very high pressures.
When they are exposed to excessive stress, they still function at their optimum best.
· Weight
An excellent heat exchanger should be lightweight so you can easily move it from one place to the other.
The best heat exchanger that is also lightweight is one made using plastic material.
Heat exchangers used in showers and swimming pools are often made using plastic for this main property.
· Capacity
The chosen device should have a varying heating/cooling capacity.
This way, the device can handle a wide range of applications.
There are heat exchangers with a cooling capacity of 2,000,000 Btu/hr and perform extremely well.
Also, it should be wide enough to hold a specific amount of fluid.
· Pressure Drops
The pressure drop of a heat exchanger depends on the needs of a customer.
You can meet the pressure drop set by a client.
That is, by lowering it.
However, this means making the device larger.
When selecting a heat exchanger, pay attention to the pressure drop factor.
· Temperature
You should consider issues such as temperature cross, temperature difference, temperature pinch, and thermal exchange coefficient etc.
This factor is most important considering you could be using the device for different applications.
There are applications requiring very high temperatures and those requiring room temperature.
· Type of Fluid Stream, Fluid Type and its Properties
There are fluids that transfer heat better than others.
For instance, liquids are better than gases.
When choosing a heat exchanger, select one that uses a liquid.
However, there are gas/gas, liquid/liquid, and liquid/gas.
Further, more heat transfer takes place when the fluid flow rate is slower.
The best heat exchanger depends on the properties of the chosen fluid.
Whether a fluid has high corrosion resistance, thermal conductivity or can withstand high pressures and temperatures is very important to this activity.
The nature of the fluids can be fouling, clean, corrosive, viscous etc.
· Ease of Maintenance
When selecting a heat exchanger, you have to consider the degree of ease of maintenance.
As a buyer, you should examine the level of maintenance of the device.
An example is the frequency of cleaning.
When checking for ease of maintenance, consider pharmaceutical exchangers, or FDA standards.
That said, when selecting a heat exchanger for your industry or application you can focus on these mentioned parameters.
Heat exchangers rely on the principles of condensation, convection, evaporation, conduction, or radiation to facilitate the heat exchange process.
Below is how the heat transfer modes work:
· Conduction
This is the transfer of thermal energy between materials that come into contact with one another.
What happens is that, when two fluids come into contact, the tube with a hot fluid transfers its heat to the cooler one making it warm/hot.
· Convection
This is a mode of heat transfer involving the movement of energy from a surface through a fluid’s motion.
The majority of fluids expand upon heating.
As a result, they become less dense and rise relative to other fluid parts that are cooler.
· Radiation
This mode of heat transfer entails the production of electromagnetic waves from a heated object/surface.
You do not need an intermediate medium to hold wave energy when using radiation.
Note: It is however important to understand that different heat exchanger:
i. Operate in different ways
ii. Use different design features, equipment and flow arrangements
Hence, the flow arrangement of a heat exchanger is important in when explaining how the device works.
Below are the flow arrangement styles:
Flow Arrangement
Some of the most common flows are:
· Parallel Flows
In parallel flow, two fluids get in the device at one end and move in parallel with one another to the other side.
· In Counter Flow
In counter-flow, the fluids get in the device from opposite ends.
This is the most efficient design.
The reason for this is because this design can transfer a high amount of energy from the heat transfer medium for every unit mass.
This is because the average temperature difference along any unit length is higher.
· Cross-flow
In a cross-flow device, the fluids move almost perpendicular to one another via the heat exchanger.
To ensure there is efficiency, these devices are specially designed to maximize the surface area of the wall between the two specific fluids.
Simultaneously, this design minimizes resistance to fluid flow via the device.
The performance of the device is also affected by the inclusion of corrugations and fins in a single or both directions.
These additions induce turbulence, channel fluid flow and increase surface area.
· Hybrid Flow
Hybrid flow occurs when a heat exchanger uses several flow passes as well as arrangements within a single device.
It is a combination of all of the other flow arrangements.
This flow is suitable for cooling/heating systems because it covers the limitations of a use/application.
These limitations include pressure and temperature requirements, budget costs or space.
Note: the only common thing among all heat exchangers is that they function to indirectly or directly expose a warmer fluid to a colder fluid.
As a result, they exchange heat.
How a Shell and Tube Heat Exchanger Work
This device transfers heat between tube bundles securely attached to a shell.
Fluids passing through the tubes give their heat to fluids that pass over tubes found in the shell.
As such, this device’s exchanger principle moves substances via a bundle of parallel tubes with heating fluid around and between fluids.
Fluid (hot) enters the device via an inlet and leaves via the outlet cold.
How Plate and Frame Heat Exchangers Work
This device works on the principle that gaskets positioned between plates lead the flow of product and colling/heating fluids via alternating channels.
Simply put, hot fluids pass over the device’s plates, and heat is transferred from the hot side to the cold side.
This process decreases the temperature of the side that is hot thereby raising the temperature of the cold side.
While heat exchangers are excellent devices used in the heating and cooling systems of machines, they have some limitations.
Some of these limitations include:
- It is very difficult to clean the pathways. To do so, you can use the mechanical or CIP system.
- There could be clogging as the pathways of the heat exchanger are narrow
- If you use aluminum alloys on a heat exchanger it increases its susceptibility Mercury Liquid Embrittlement Failure
- Pressure drop is a common problem in heat exchangers. If there is pressure drop in the device you have to check every plate for this fault.
- It is very difficult to repair or prevent leakage in the device. There are devices that have to be taken apart entirely to check and correct a leak.
- The initial cost of heat exchangers is high. For instance, plate heat exchangers are expensive due to titanium plates.
Shell and Tube heat exchangers are not as expensive as the plate exchangers.
- There are some devices that require more space than the other.
For example, shell and tube heat exchangers require more space than plate exchangers.
Of course, no.
Heat exchangers come in different sizes depending on the intended purpose, a client’s preferences or cost.
Size variations occur on different aspects such as on the:
- Pipes
- Surface area of the device in square meters
- General device size
You do not want to buy a heat exchanger that will not fit the designated physical space because it is too big.
If you are buying a heat exchanging device, get one that leaves room for future expansion.
Refrain from purchasing a device that fully occupies the physical space.
Compact heat exchangers are suitable for applications with limited space like automobiles or airplanes.
These devices provide high heat efficiencies in more light-weight and smaller solutions.
Further, these devices have high heat transfer surface area to volume ratios.
If you are using the device for a liquid-to-gas application, the ratio will be ≥400 m2/m3.
However, if it is gas-to-gas application the ratio will be ≥700 m2/m3.
Some variants of heat exchangers that are used for applications with limited space are plate heat exchangers.
You can find this device almost everywhere, in all types of places.
It can be used in cooling or heating buildings, helping machines and engines to work well.
An energy-efficient shower has a heat exchanger often installed in the outlet of the wastewater.
This device has copper coils attached to the heat exchanger.
They help with heating the water.
Cold water moves up the plug to the heat exchanger where it is heated.
It does not mix with dirty water but it picks some of its heat from the waste water flowing through the other pipe of the plug.
Air conditioners and refrigerators remove heat from one compartment where it is not needed.
Then, they pump it in a fluid to another place where it can be dumped.
The cooling fluid is often fully sealed in a set of pipes so it does not come into contact with the air.
In engines and power plants, heat exchanger helps in eliminating excess heat.
The machine uses the heat transfer process to achieve this goal.
Heat exchangers are made with different types of materials.
These materials provide various properties which are responsible for the efficiency and functionality of the device.
They have to withstand high stress conditions all through the heating and cooling process.
Considering that you may have to use high pressure, temperature and corrosive fluids, the materials must be suitable to meet these requirements.
The three main class of materials used to make this equipment are:
Flow chart for heat exchanger system
· Ceramics
This material can withstand high temperatures.
It is, therefore, good for high-temperature applications.
You can use ceramics, especially with abrasive and corrosive fluids at low or high temperatures.
· Graphite
This material has high corrosion resistance and thermal conductivity
· Composites
They exhibit corrosion resistance and high thermal conductivity.
Also, they have reduced weight making them portable.
Composites take the best features of their parent material.
· Plastic
Although the low cost has high thermal conductivity and can maintain a moderate corrosion resistance degree.
Plastic can also resist fouling and they weigh less.
They are mechanically weak and can degrade over time.
This material is a good choice for a shower or swimming pool operating at room temperatures.
· Metals
Metals can withstand high pressures and temperatures as well as have high thermal conductivity.
Some of the metals are as shown below:
- Stainless steel 316L/304/others
- Carbon Steel
- Aluminum alloys
- Titanium
- Copper
- Brass
- Duplex
- Cupro-nickel
- Hastelloy
Typically, heat exchangers are sold at competitive prices.
The prices of this device vary depending on factors such as the size, design, shape, type, and material used.
The overall cost of this equipment includes price, production, material, installation, operational, and maintenance costs.
A single piece of the heat exchanger can cost up to around $6,000.
For instance, a shell and tube heat exchanger with a heating/cooling capacity of 2,000,000 Btu/hr, maximum temperature of 3000C and a minimum temperature of -20C costs $2,556. 88.
The initial price is high but a more durable device lead to lower maintenance costs.
As a result, a buyer spends less costs over the lifespan of the product.
On the other hand, for a cheaper heat exchanger, you will spend less money at the beginning.
However, you can spend more money over the lifespan of the product because of replacements and repairs.
This equipment has different cooling capacities which depend on the particular type of heat exchanger.
A cooling capacity can range from as low as 5,000 Btu/hr to as high as 2,000,000 Btu/hr.
The Btu/hr cooling capacity is often based on a 10 psi pressure difference, 85° F water and 180° F process water.
The cooling capacity of your heat exchanger will however depend on a customer’s need or application requirements.
Whenever you want to buy a heat exchanger, as a customer you select what fits your application needs.
To do this, you will have to focus on the features of this device.
Some of the features of heat exchangers that you can look out for when buying this device are:
- They are easy to clean due to the appropriate sizes of the device’s diameter
- They can withstand high pressures and temperatures
- Are versatile as they are used in different chemical process applications
- They come in different sizes; there are no size limitations when it comes to heat exchangers.
You may find a small, medium, or large-sized devices depending on your application.
- Availability of spare parts; sometimes it is good to have spare parts just in case the machine breaks down and there has to be repaired.
- Excellent thermal conductivity
- Have corrosion resistance; this device may be exposed to fluids that are acidic or which generally corrodes the surfaces.
It is important to select equipment that is made with a material which is corrosion-resistant.
- Use fluids of different viscosity
- Have fouling characteristics
- Availability of water-soluble compounds
- Particulate matter content
- Has a proper design
- Highly durable; a device that is durable is made with materials such as stainless steel that has high tensile strength.
- High efficiency
- Sturdy construction; a device has to be strong enough to support its components. Its sturdiness also gives the device an excellent appearance.
- Low maintenance; this device must attract low maintenance costs. And, if there has to be maintenance it should be low because it is specially designed to be durable, high quality and efficient.
Here are some of the benefits of heat exchangers:
· Utility Consumption by Conserving Steam, Electricity and Water
You can save energy with heat exchangers.
The heat from the incoming fluid heats the fluid exiting the device then it is cooled.
As a result, there is transfer efficiency which saves energy and heating.
Often, this process is referred to as heat recovery/regenerative heat exchange.
You do not have to use energy to heat fluids through the different outlets/tubes.
The tubes will share their energy from the fluids to the fluid in the other tube through convection/conduction.
· Clean-in place/Maintenance
For the majority of the heat exchangers you do not have to dismantle/open them when cleaning its parts/components.
What happens is that the device heats the solutions or cleaning water to a consistent temperature.
This helps in the residue removal.
You can use chemical cleaning in place (CIP) while maintaining the device.
Similarly, you can use mechanical cleaning for the maintenance of the device.
Mechanical cleaning involves using a jet of pressurized water via fast-opening ports without necessarily dismantling the pipes.
As such, maintenance is very simple.
· Unique Design
A Heat exchanger has unique design features.
That is, almost perfect counter-current coupled with unequal fluid flow rate on the two sides of the device.
There are different flow areas combined with no points of contact especially for the more fouling fluid.
· Efficiency
This device is highly efficient, especially when it has a hybrid flow arrangement.
With this design, it can work at its optimum best with limited issues.
Considering that the device has undergone several inspection and quality tests, it has limited shortcomings.
For instance, the device does not have any leakages, corrosion, erosion of surfaces or breakage.
The device, therefore, functions at its best when in use in an application.
· Cost
Contrary to the past when heat exchangers were bulky and costly, today, they are affordable.
They are sold at very competitive prices to the customers.
You can find portable heat exchangers even for home setting or any other place.
Some devices cost as low as $500 while others cost as high as $7,000.
The cost depends on the design, type, flow arrangement and size etc.
You can choose from any of the following types of heat exchangers:
Shell and Tube Heat Exchanger
This equipment is mostly applicable in high-pressure applications.
It functions at a temperature higher than 2600C, and 30 bar pressure.
Shell and Tube Heat Exchanger is made using durable material that can sustain the high pressure and load.
This device includes several tubes that are arranged longitudinally in the casing.
A specific fluid is passing through the tubes and another fluid passing over the tubes via the shell opening.
hell and tube heat exchanger
However, all of the tubes are connected to a single inlet or outlet via the first fluid pass.
The second fluid is passing over the tubes as there are baffles inside the casing.
They help to optimize the contact of the second fluid with the tubes.
The tube and shell come in different designs and shapes.
While a smaller diameter makes the heat exchanger compact and economical, it is important to have a proper diameter size.
That is, not too large or too small.
Baffles in this device aid in the direction of fluid flow across the tubes.
The baffles also prevent the tubes from vibrating.
They also provide turbulence in the fluid flow within the casing which leads to higher heat transfer coefficient for the outer surface of the tubes.
Plate Heat Exchangers
Plate and tube heat exchanger
It is made of several thin and slightly separated plates that have small fluid flow passages and large surface areas for heat transfer.
This is heat exchanger is more practical due to the new technology used in making gasket and brazing.
You can access a permanently bonded device or an easily assembled and disassembled one.
This device comes in different designs and configurations of plates.
It can be used in HVAC, refrigeration, and cooling applications.
Plate and Shell Heat Exchanger
Plate and shell heat exchanger
Basically, this device is a combination of shell and tube heat exchangers with plates.
It involves mounting plates on a shell.
Multiple plates are joined together to facilitate better heat transfer.
The plates of this device are often made using stainless steel of very high-quality materials.
Further, these plates are hanged vertically in the casing.
They are also corrugated to provide points of support enhancing heat transfer.
The plates in this equipment have a circular cross-section.
They are welded together to fit in the casing.
The device, therefore, offers high heat transfer at high pressure and temperature.
Also, the main advantage of this equipment is the gasket which offers protection.
This component provides protection against leakage which may occur in high pressures and temperature.
Secondly, the device is structured in such a way that the full pack of plates often assembled into the outer shell.
This develops a secondary flow path via the shell side.
Adiabatic Wheel Heat Exchanger
Adiabatic wheel heat exchanger
This heat exchanger uses a solid store or intermediate fluid to hold heat.
This heat is then passed to the opposite side of the heat exchanger.
Consequently, it is released as heat to become cool.
An adiabatic wheel heat exchanger has a large wheel with good threads rotating all through the cold and hot fluids.
Of course, this is alongside fluid heat exchangers.
Plate and Fin Heat Exchanger
Plate and fin heat exchanger
This equipment has a pack of fins often arranged in offset, straight and wavy form to enhance its effectiveness.
Depending on the requirements of the device, the flow can be counter or cross flow.
An excellent Plate and fin heat exchanger is made of aluminum alloys.
They reduce the overall weight of the device.
Its application is a low-temperature applications such as helium, natural gas, oxygen and aircraft industries like aircraft and motor engines.
The large heat transfer area of the plate fins results in its heat transfer efficiency.
This device can also withstand high pressures.
It has a narrow pathway that may cause clogging in the device.
Cleaning such a clog is also often difficult.
Pillow Plate Heat Exchanger
Pillow plate heat exchanger
This device consists of a thin sheet of the metal spot.
It is welded to the surface of another metal sheet which is often thicker than the latter.
There is a thin plate that is welded in a regular pattern consisting of dots.
Following the welding process, the enclosed space is pressurized with an external force that causes the remaining thin metal to bend outwards around the welds.
This process also provides space for the device’s fluid to flow.
This heat exchanger is often used in the dairy industry, especially for the cooling of milk.
Fluid Heat Exchangers
Fluid heat exchanger circuit
This is a type of heat exchanger that functions on the principle that gas moves upwards via a shower of water.
Then the water is transferred somewhere else before it is cooled.
Fluid heat exchangers help with cooling gases while simultaneously removing impurities.
This device is commonly used in espresso machines.
Waste Heat Recovery Units
This heat exchanger recovers heat from a stream of hot gases while passing it to a working medium such as oils or water.
Waste heat recovery unit
Dynamic Scraped Surface Heat Exchanger
This device is often used for cooling or heating with crystallization processes, high-viscosity products, high-fouling and evaporation processes.
The continuous scrapping of the surface is done by the long-running times.
Hence, avoiding fouling and managing a sustainable heat transfer rate during the heat exchange process.
Phase-Change Heat Exchangers
This equipment has multiple uses; it can work as an evaporator or condenser.
You can use it in refineries, nuclear and chemical plants.
Direct Contact Heat Exchangers
This machine involves heat transfer between cold and hot streams of two phases in the absence of a separating wall.
For direct contact heat exchangers, there are three main types:
- Immiscible liquid – liquid
- Gas – liquid
- Solid-liquid or solid – gas
This heat exchanger is mostly used in the humidification, air conditioning, water cooling and condensing plants and industrial hot water heating.
With this device, heat is transferred between a liquid and gas in the form of sprays, films, or drops.
Microchannel Heat Exchangers
This equipment involves fluid flow in lateral confinements with dimensions of below 1mm.
Microchannels act as confinements.
It is made using materials such as ceramics, metals or low-cost plastic.
This heat exchanger is used in applications such as:
- Heat Recovery Ventilators
- Air Conditioning
- Heat Pumps
- High-Performance Aircraft Gas Turbine Engines
Evaporators, Condensers and Boilers
These are heat exchangers which use a two-phase heat transfer mechanism.
What happens in two-phase heat exchangers is that one or more fluids go through a phase change during the process of heat transfer.
Fluids change from liquid to gas or from gas to gas, or liquid to liquid.
Condensers, Boilers and Evaporators
The others, evaporators and boilers, have a heat transfer process which changes fluids from liquid form to vapor or gas.
Condensers take heated vapor or gas then cool it until it undergoes condensation changing from vapor or gas to liquid.
All these different types of heat exchangers are excellent.
They are however suitable for different applications.
You should trade with caution when selecting a device for your application.
Choose one which will be suitable for fulfilling your goals/needs.
The warranty of this device varies depending on its supplier/manufacturer.
There are heat exchangers with a 2/1-year warranty to mainly cover manufacture defects.
If the device has any manufacture defects within the 1-2-year period, you can return it back.
This warranty date starts on the SAT.
However, not later than 24 or 36 months from the date of delivery of the device to the end user site.
The warranty does not cover any physical damages caused by the client.
In the event that such damages occur, it is up to the client to pay for the repairs.
You need a heat exchanger system that is efficient, reliable, safe and durable.
To do this, you have to create special designs which reflect specific considerations/needs.
Below is how to design a heat exchanger:
The design of this device involves three key phases.
But first before delving into this area, you have to explore the sizing of heat exchangers.
First and foremost, you have to consider several thermal phenomena before designing a heat exchanger.
They include:
Thermal Radiation that can be Negligible.
Conduction; it is based on the idea of thermal agitation that takes place without material movement.
It is defined as the natural movement of heat from plates, walls and tubes.
Forced convention of both fluids; It is the movement of heat across a wall and passing fluid, both in different temperatures.
In this device, forced convection of the two fluids is as a result of artificial circulation.
Phase 1: Technology Choice
The choice for the best technology depends on the below factors:
- Limitation of maintenance and installation (easy to clean and install)
- Application
- Nature of the fluids (fouling, viscous, anti-corrosive etc)
- Thermal program (these are required efficiency and temperatures)
You can know the type of Heat Exchanger you want by taking all these factors into consideration.
Phase 2: Thermal Design
When conducting thermal design, there are three main activities you have to complete.
Thermal Program Validation
This process involves determining the device’s geometry, size or power.
You have to validate this data using the below formula:
Thermal design validation
Looking at this example, the answer is below.
Tout = 73°C
Therefore, the total power is 65,000 KCal/h or 756 KW
Heating Surface Calculation
Before anything, you have to calculate the Logarithmic mean temperature difference.
It is the logarithmic average of the heat exchanger’s temperature differences at every end.
After calculating power and LMDT, then you can calculate heat exchange using the below formula.
S = heating area (m2)
K = Heat Transfer Coefficient in KW/°C/m2.
This is particular to every equipment and provided by the manufacturer.
Incrustation and K Calculation
You have to find heat transfer coefficient as it helps in finding the heating area and the subsequent sizing of the heat exchanger.
From this formula, the transfer coefficient is shown by h1 and h2
Phase 3: The Heat Exchanger Pressure Drop Calculation
Energy loses arise from a moving fluid, and this is due to mishaps such as baffles or friction on the walls.
Pressure drop is how loss of energy is often expressed.
For the fluid to flow, the loss in energy has to be compensated.
When designing a heat exchanger, you have to calculate the pressure drop using different correlations decided by the exchange surface’s characteristics.
The efficiency of a heat exchanger equates to this formula:
It is close to impossible obtaining a yield of 100%.
The yield is dependent on the client’s needs/specifications, that is, temperatures and power needs.
On the other hand, the effectiveness of this machine equals to 1.
All these factors help in calculating the rating and sizing of the heat exchanger during design optimization.
The calculations center on shell thickness, tube-sheet thickness, gasket sizing and other component measurements.
Often, when designing an excellent heat exchanger for a specific application, you have to determine three main things.
They include the heat transfer co-efficient, temperature change of the fluids, and the overall construction of the device.
These factors are then compared to the rate of heat transfer as shown above.
Heat exchangers are equipment often used all through industries for heating and cooling processes.
Some of the applications include:
- Cooler
- Condenser
- Crude oil cooling
This device functions as a heat exchanger between the residue that gets into the cooler and crude oil that enters the furnace.
This process helps ensure that the energy in the residue can be used to raise the crude oil temperature.
Thereby, making the load of the furnace lighter.
Often, a Shell and Tube Heat Exchanger is the best device for this application.
Evaporator
In every industrial process, you must find an evaporator.
This is a device used in the evaporation of solutions.
The goal of evaporation is to concentrate on a solution that has solutes that are not volatile with other volatile solvents.
Reboiler
This device is attached to a distillation column.
It produces mainly steam for fractional distillation separation.
It functions similarly to a condenser leading to a liquid reflux which is brought back to the distillation column.
Reboilers, therefore, generate heat flow for distillation and other similar chemical processes.
Vaporizer
Vaporizers help in the evaporation of liquids.
The device produces steam which is utilized for chemical processes.
It does not work as a heat source in the same way that steam does.
A vaporizer is, therefore, an important component of a machine that vaporizes volatile liquids anesthetics.
Chiller
A chiller moves heat from a liquid via cooling-absorption cycles or compression-vapor.
This equipment has four main parts; condenser, evaporator, compressor, and different forms of metering devices.
It has multiple refrigerants.
The refrigerant for absorption chillers is municipal water while the desiccant is benign silica.
Airfin Cooler
This device helps with the fluid cooling process with use of air flowing via a fan.
Airfin cooler is better than a Shell and Tube Heat Exchanger.
With an Airfin cooler, you do not need other complementary facilities that you would require were you to use a Shell and Tube Heat Exchanger.
Double Pipe Exchanger
This equipment consists of double pipes (a small and big pipe) and concentrated tubes.
Typically, a double pipe exchanger has two legs that are connected together.
This device can manage high-pressure fluid on the sides of the tube.
It has a configuration that allows for this property.
Besides, this device can be assembled with standard pipes.
However, some of the well-known industries in which this device in used are:
- Refrigeration
- Waste water treatment
- Beer and wine making
- Nuclear power
- Petroleum refining
- Petrochemical plants
- Oil refining
- Food processing
- Chemical processing
- Aircraft
- Power generation
- Cryogenics
Heat exchanger diameter
The diameter of heat exchangers varies depending on the design, type, shape or size of the device.
Diameter is often measured in inches.
In most cases, it is referred to as the head diameter.
A typical heat exchanger can have a head diameter as large as 15 inches, and as small as 1 1/8 inches.
A head diameter increases in size proportionately to the heating/cooling capacity measured in Btu/hr.
For instance, a Brass Shell and Baffled Copper Tube of a cooling capacity of 130,000 Btu/hr will have a head diameter of 43/16 inches.
Similarly, a Brass Shell and Baffled Copper Tube of a cooling/heating capacity of 2,000,000 will have a head diameter of 93/4.
The same occurs for other types of heat exchangers.
Now, that’s all for this guide on the heat exchanger system.
Remember, depending on your specific needs, there is always a heat exchanger that meets your unique performance requirements.
For any questions or inquiries, contact FilSon Filter team now.